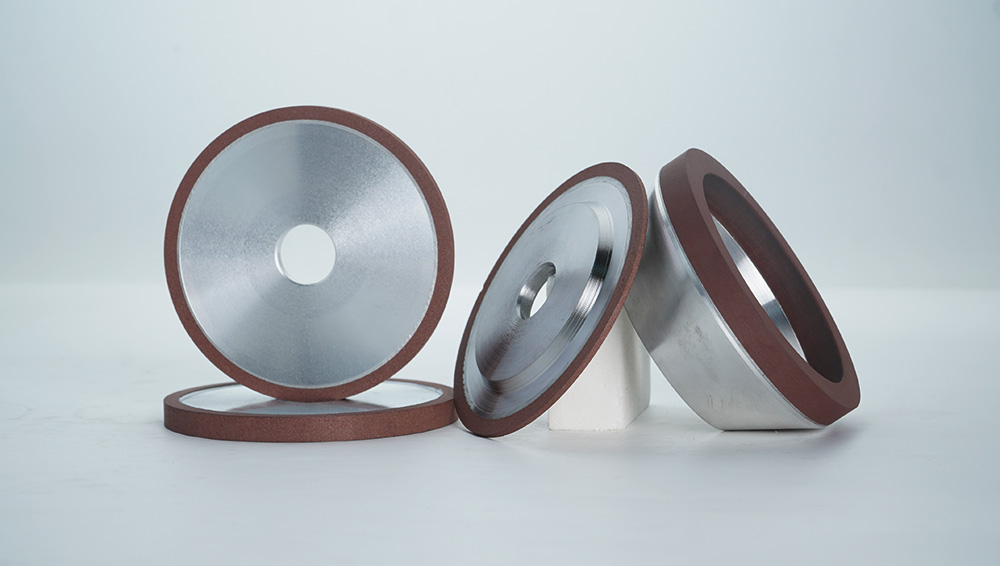
Knowing the crucial differences between diamond and CBN grinding wheels exists for ensuring the right selection of a tool for your grinding tasks. Both have specific distinguishing properties are appropriate for the particular applications they have. Now take a closer look at these differences.
Table of Contents
Diamond Grinding Wheel
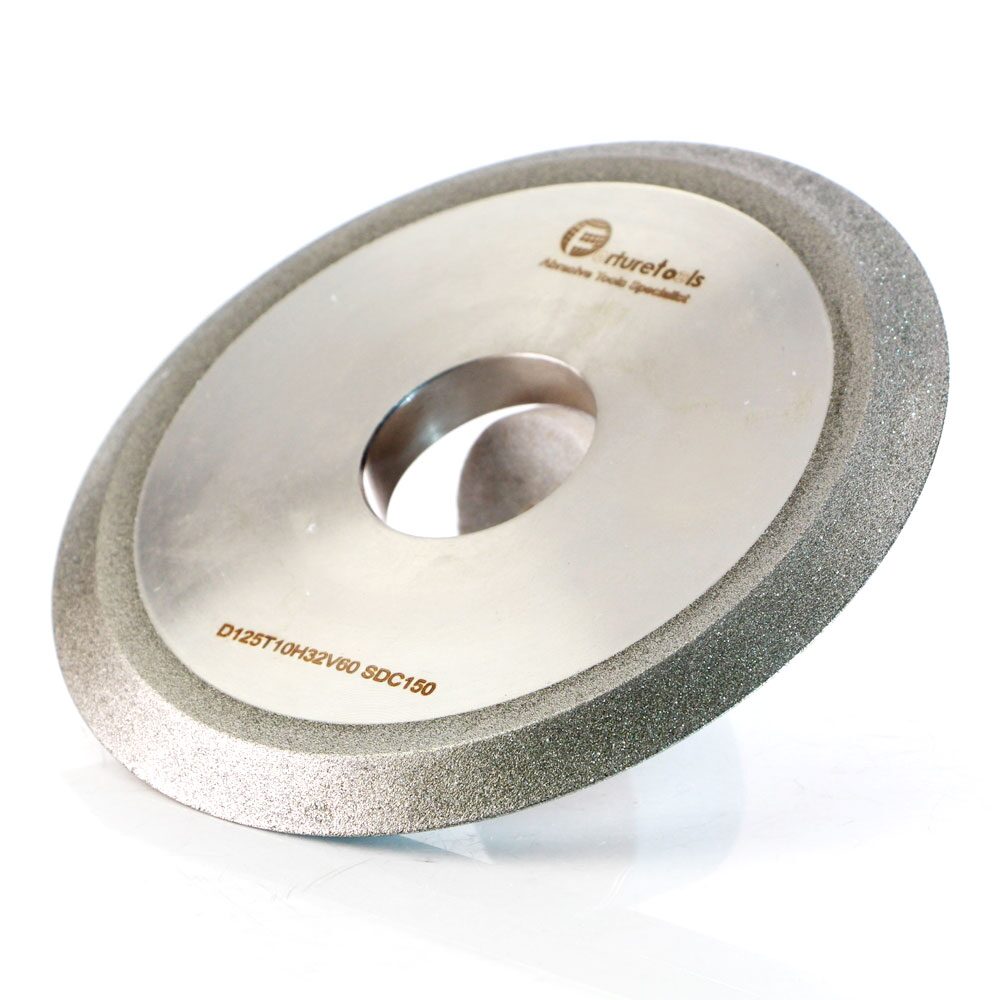
Diamond is made of pure carbon atoms arranged in a specific crystal structure. This structure gives diamond its unmatched hardness, which is what makes it such a powerful cutting tool. You’ll find two main types of diamond used in grinding wheels: natural and synthetic. Both offer exceptional hardness, but synthetic diamonds are more commonly used in industrial applications due to their consistent quality and availability.
Unlike a CBN grinding wheel, diamond’s claim to fame is its incredible hardness. It’s the hardest known natural material, making it capable of cutting through materials that would leave other abrasives scratching their heads. This hardness allows diamond wheels to tackle tough jobs with ease. It also has a surprising amount of toughness. This means it can withstand the shocks and stresses of the grinding process without chipping or breaking.
You’ll find diamond grinding wheels hard at work in a variety of industries. They’re the go-to choice for grinding hard and brittle materials like ceramics, glass, stone, and tungsten carbide. For example, in the electronics industry, diamond wheels are used to shape and polish delicate components. In the construction industry, they help shape and finish stone and concrete. And in the automotive industry, they’re used to grind hardened steel parts.
CBN Grinding Wheel
CBN, or cubic boron nitride, is another superabrasive material used in grinding wheels. While not as hard as diamond, CBN boasts exceptional thermal stability and resistance to chemical reactions. This makes it ideal for grinding ferrous materials, which can react with diamond at high temperatures.
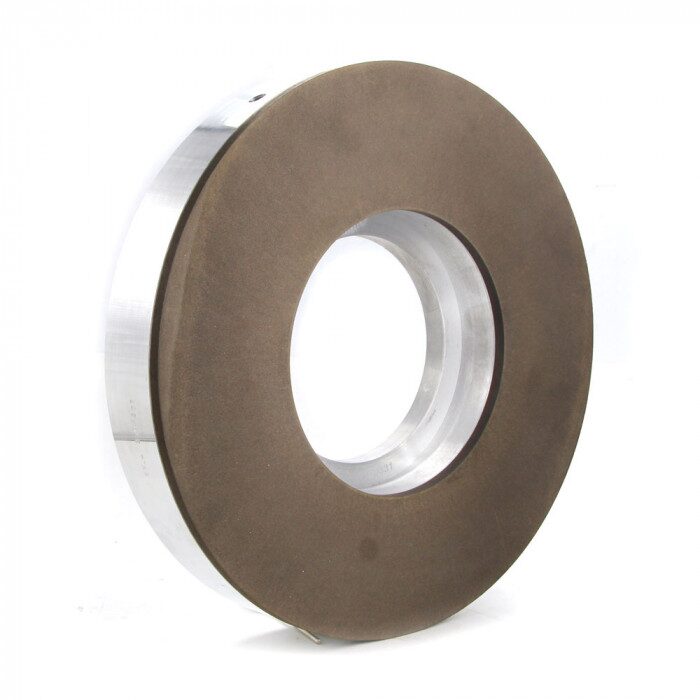
CBN grinding wheels shine in applications involving hardened steels and superalloys. Their ability to withstand high temperatures without deteriorating is invaluable in these demanding environments. You’ll commonly find CBN wheels in the automotive, aerospace, and energy industries.
Material Compatibility
Diamond grinding wheels are perfect for working with non-ferrous materials. You can use them on ceramics, glass, and other non-metallic substances without worrying about chemical reactions. Diamond’s hardness and ability to produce fine finishes make it the go-to choice for these materials.
CBN grinding wheels are the champions of ferrous materials. They effortlessly handle hardened steels and superalloys. Their resistance to heat and chemical breakdown ensures consistent performance and long tool life when working with these tough metals.
Performance Characteristics
Diamond grinding wheels are renowned for their exceptional wear resistance. They hold their edge for longer than other abrasives, resulting in less frequent dressing and higher productivity. Additionally, diamond’s high thermal conductivity helps dissipate heat generated during the grinding process, reducing the risk of workpiece damage.
CBN grinding wheels stand out for their remarkable thermal stability. They can withstand high temperatures without losing their cutting ability, making them ideal for demanding applications. CBN is also chemically inert, meaning it won’t react with the workpiece material, ensuring consistent performance and preventing contamination.
Grinding Efficiency
Diamond grinding wheels are the preferred choice when precision and a fine surface finish are paramount. Their ability to produce sharp cutting edges allows for delicate material removal, resulting in exceptional surface quality. This makes them ideal for applications like polishing, honing, and finishing operations where accuracy is critical.
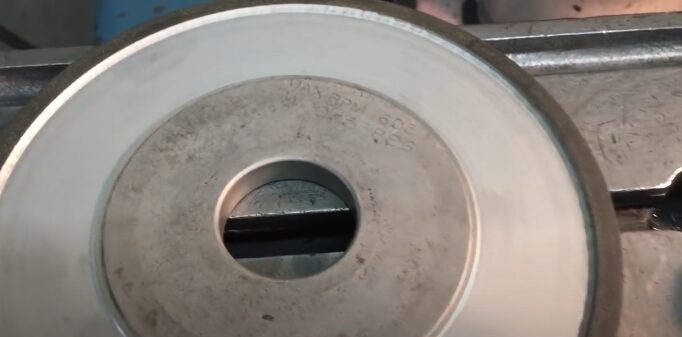
However, while diamond excels in precision work, it may not be the most efficient option for aggressive stock removal. For tasks demanding high material removal rates, CBN grinding wheels often take the lead. CBN’s robust cutting action allows it to tackle heavy-duty grinding jobs with ease. You’ll find CBN wheels particularly effective in applications like roughing, shaping, and deburring, where speed and efficiency are essential.
It’s important to note that while diamond is generally slower for material removal, it can still be used for roughing operations under specific conditions. For instance, when grinding hard and brittle materials, diamond’s ability to cut cleanly can prevent work hardening and improve overall efficiency.
Similarly, a CBN grinding wheel can be used for finishing operations, but its performance may not match that of diamond in terms of surface quality. However, for applications requiring both high material removal and a decent finish, CBN can be a viable option.
Cooling and Lubrication
Proper cooling is essential when using diamond grinding wheels. Diamond generates heat during the grinding process, which can lead to thermal damage to both the wheel and the workpiece if not managed effectively. Using coolant helps to dissipate this heat, preventing wheel failure and improving the quality of the finished surface.
While CBN is less susceptible to thermal damage due to its superior heat resistance, using coolant still offers several advantages. Coolant helps to reduce friction, which extends the life of the grinding wheel. Additionally, it washes away chips and debris, improving cutting efficiency and preventing wheel loading. By using coolant with CBN wheels, you can optimize their performance and achieve better results.
Tooling and Maintenance
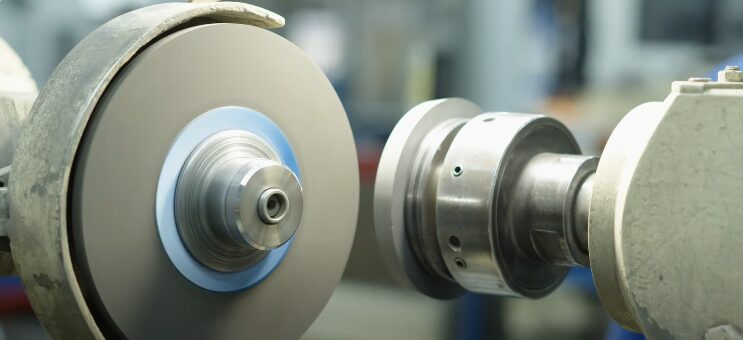
Working with diamond grinding wheels requires special tooling and care due to their exceptional hardness. You’ll need specialized equipment to dress and true the wheel, as traditional dressing tools might not be sufficient. Regular inspection for wear and damage is crucial to ensure optimal performance and safety.
While CBN grinding wheels are less demanding in terms of tooling, proper handling and storage are essential to maintain their performance. Avoid dropping or subjecting the wheels to excessive shock, as this can damage the abrasive grains. Storing them in a clean, dry environment will help prevent contamination and prolong their lifespan.
Conclusion
Choosing between a diamond and CBN grinding wheel depends on the specific material you’re working with, the desired finish, and your budget. By understanding the strengths and weaknesses of each, you can make an informed decision that optimizes your grinding process. Whether you prioritize precision and surface quality or speed and efficiency, there’s a grinding wheel out there to meet your needs.