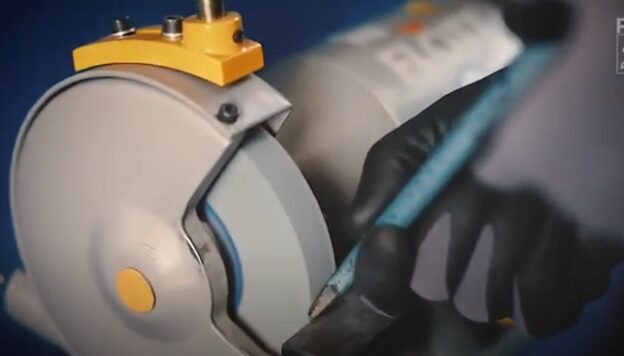
Understanding Grinding Wheel Performance is crucial. It impacts efficiency, quality, and safety in grinding operations. Several factors influence a grinding wheel’s performance. Let’s explore them.
Table of Contents
Abrasive Material
The type of abrasive in a grinding wheel significantly impacts its performance. Aluminum oxide is common for general-purpose grinding, while silicon carbide excels on hard, brittle materials. Diamond and CBN (Cubic Boron Nitride) are premium abrasives for exceptional performance on tough materials.
Abrasive grain size also matters. A coarser grain removes material faster but creates a rougher finish. A finer grain produces a smoother finish but removes material slower. You must balance material removal rate and surface finish when selecting grain size.
Bonding Agent

The bonding agent in a grinding wheel holds the abrasive grains together. Different bond types offer distinct advantages. Vitrified bonds, made from glass, are strong and durable for various grinding applications. Resinoid bonds, using synthetic resins, offer fast cutting action and good for cool grinding. Metal bonds, with a metal matrix, are ideal for high-pressure grinding and provide excellent wheel strength. Hybrid bonds combine properties of different bond types for specific applications.
When choosing a bond, consider the strength needed. A strong bond holds the abrasive grains firmly, resulting in slower wheel wear but reduced grinding efficiency. Conversely, a weaker bond allows for faster grinding but increased wheel wear. You’ll need to find the right balance for your grinding operation.
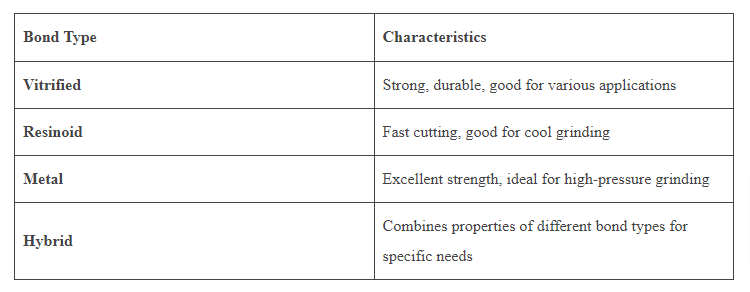
Wheel Structure
You’ve probably noticed that grinding wheels aren’t solid blocks of material. They have tiny holes, or pores, throughout. These pores are essential for your grinding wheel’s performance. They allow coolant to flow through the wheel, helping to cool the grinding area and prevent overheating. Additionally, pores help to carry away chips and debris, stopping them from clogging the wheel. This keeps the wheel cutting efficiently.
Another important factor in wheel structure is density. This refers to how tightly packed the abrasive grains and bonding material are. A denser wheel typically removes material faster but can generate more heat. On the other hand, a less dense wheel might produce a better surface finish but remove material slower.
Grinding Parameters
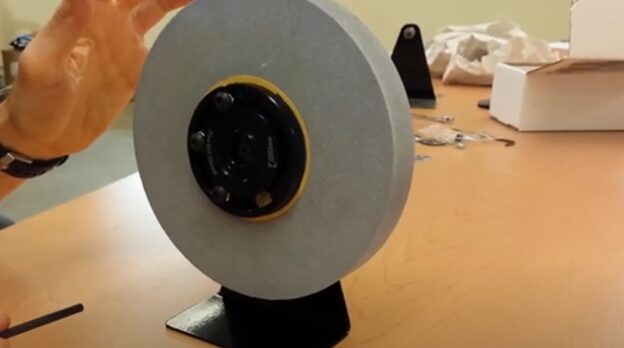
Grinding Speed
Grinding speed, or how fast the wheel spins, significantly impacts your operation. A higher speed usually means faster material removal. But be careful! Too high a speed can overheat the wheel, causing it to wear out quickly and reduce its effectiveness. On the other hand, a slower speed might produce a better surface finish but take longer to remove material.
Feed Rate
The feed rate is how quickly the workpiece moves into the grinding wheel. A faster feed rate generally removes material quicker but can also create more heat and stress on the wheel. This can lead to a rougher surface finish and reduced wheel life. Conversely, a slower feed rate produces a better surface finish but slows down the grinding process.
Depth of Cut
How deep the wheel cuts into the material is called the depth of cut. Taking deeper cuts removes material faster but increases the risk of wheel damage and burning the workpiece. A shallow depth of cut is safer for the wheel but takes longer to finish the job.
Coolant and Lubrication
Coolants help manage the heat generated during the grinding process, preventing damage to the workpiece and the wheel. They also help to lubricate the grinding contact, improving the surface finish and reducing friction. The type of coolant you use depends on the material you’re grinding, the wheel type, and the desired outcome.
The amount of coolant you use also matters. Adequate coolant flow effectively cools the grinding zone, extending wheel life and preventing workpiece damage. However, too much coolant can wash away the abrasive particles, reducing grinding efficiency. Finding the right balance is essential for optimal performance.
Workpiece Material
Harder materials require tougher, more durable wheels. You’ll likely need a coarser grit and a faster speed to remove material efficiently. Softer materials, on the other hand, can be ground with finer-grit wheels and slower speeds to achieve a better surface finish.
Tough materials produce larger chips during grinding, which can put more stress on the wheel and increase wear. You might need a more open wheel structure to allow for better chip clearance. Additionally, you may need to adjust your grinding parameters to accommodate the material’s toughness.
Machine Conditions
The type of grinder you use impacts how you approach the grinding process. Surface grinders are designed for flat surfaces, while cylindrical grinders handle round parts. Other types, like centerless grinders, have specific applications. Understanding the capabilities and limitations of your grinder is crucial for optimal results.
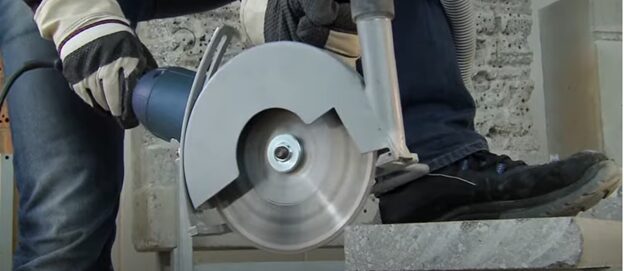
A rigid machine is essential for accurate and consistent grinding. Vibrations can cause dimensional inaccuracies and poor surface finish. A sturdy machine base and well-maintained components contribute to overall rigidity. Regular checks and maintenance are necessary to ensure your grinder operates at its best.
Operator Skill and Experience
Proper training is essential for safe and efficient grinding. Understanding grinding wheel characteristics, machine operation, and safety procedures is crucial. Well-trained operators can set up the grinding process correctly, operate the machine safely, and perform necessary maintenance tasks.
Constant attention to the grinding process is key. Experienced operators can recognize when adjustments are needed. By monitoring factors like wheel wear, workpiece temperature, and surface finish, you can make necessary changes to grinding parameters or coolant flow. This helps maintain consistent quality and efficiency throughout the operation.
Environmental Factors
Environmental conditions can affect your grinding process. High temperatures can cause the grinding wheel to expand, affecting its balance and performance. Humidity can impact the effectiveness of your coolant, reducing its cooling ability. Consider these factors when setting up your grinding operation, especially in environments with extreme conditions.
Grinding generates dust and debris, which can contaminate your grinding wheel and affect its performance. Dust can clog the wheel’s pores, reducing its cutting efficiency. Additionally, it’s a health hazard for operators. Proper ventilation and dust collection systems are essential to protect both your equipment and your workers.
Maintenance Practices
Over time, your grinding wheel will wear down and lose its shape. Dressing and truing are processes that restore the wheel’s original profile. Dressing removes small amounts of material to expose fresh abrasive grains, while truing corrects any irregularities on the wheel’s face. Regular dressing and truing are essential for maintaining optimal cutting performance and preventing damage to the workpiece.
Proper storage is crucial for preserving your grinding wheels. Store them in a cool, dry place away from direct sunlight and extreme temperature fluctuations. Avoid stacking wheels on top of each other, as this can damage the edges. Additionally, protect wheels from dust and debris to prevent contamination. By following these guidelines, you can extend the life of your grinding wheels.
Conclusion
The knowledge you have acquired through testing different abrasives is important for effectively using such materials. The knowledge is helpful in several ways, it helps in the selection and proper utilization of the grinding wheel. This way, the user is going to improve efficiency, quality of the product, and safety on the operator in the grinding operations. The skills you gather by handling different abrasives and using the data will make your work a lot more efficient.