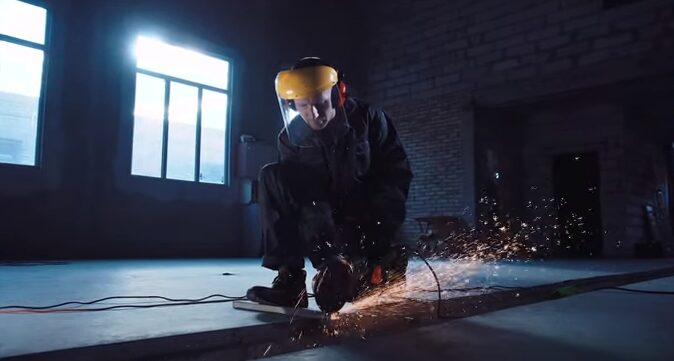
Understanding the distinctions between rough grinding and precision grinding is essential in manufacturing. Each type serves a unique purpose in industrial processes. Rough grinding focuses on removing large amounts of material quickly. In contrast, precision grinding aims for exact dimensions and fine surface finishes. Knowing these differences helps you choose the right method for your specific needs.
Table of Contents
Rough Grinding
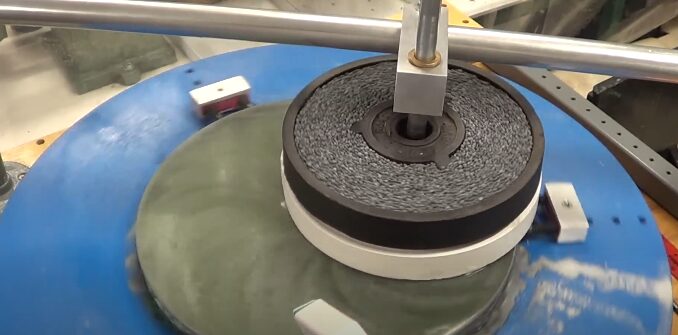
Rough grinding primarily functions to remove excess material from a workpiece. This process is crucial in preparing the material for further refinement. You can think of it as the first step in shaping a part. It does not prioritize accuracy or surface finish. Instead, it emphasizes quick stock removal. This makes it ideal for initial shaping tasks in various manufacturing sectors.
The material removal rate in rough grinding is significantly high. This means that rough grinding can quickly achieve the desired shape or size. You can expect to see substantial amounts of material being removed in a short time. This efficiency is vital in industries where time is money. The focus here is on productivity rather than precision.
Typically, rough grinding leaves a rough or coarse surface finish. This finish is not suitable for applications requiring tight tolerances. However, it is acceptable for subsequent processing steps. You should be aware that the rough surface can be improved later through precision grinding. Therefore, while rough grinding is not about aesthetics, it is a critical step in the overall manufacturing process
Precision Grinding
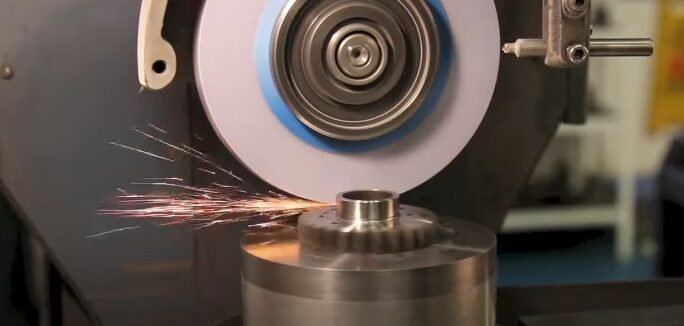
Precision grinding focuses on achieving exceptional accuracy and a high-quality surface finish. It’s about creating parts with exact dimensions and smooth surfaces. This process is crucial for components used in industries like aerospace, automotive, and medical equipment, where tolerances are extremely tight.
Accuracy and tolerance are paramount in precision grinding. You need to consistently produce parts that meet specific dimensional requirements. The surface finish is equally important. It affects the part’s performance, durability, and appearance. Precision grinding aims for surface finishes that are smooth and free of defects.
There are several types of precision grinding processes:
- Surface grinding is used to create flat surfaces on workpieces.
- Cylindrical grinding is ideal for creating cylindrical shapes with high accuracy.
- Centerless grinding is a specialized method for grinding long, slender parts without using a workpiece center.
Grinding Parameters
Depth of cut refers to how much material is removed with each pass of the grinding wheel. In rough grinding, you can use a deeper depth of cut to remove material quickly. However, in precision grinding, the depth of cut is much smaller. This ensures that you gradually remove material without causing damage to the workpiece.
Feed rate and speed also play a crucial role in grinding. Feed rate is how fast the workpiece moves past the grinding wheel. In rough grinding, you can use a higher feed rate to increase material removal. But in precision grinding, the feed rate is much slower to maintain accuracy and control. The rotational speed of the grinding wheel also affects the grinding process. A higher speed can increase material removal but can also generate more heat, so it’s important to find the right balance.
Coolant is essential in precision grinding. It helps to control the heat generated during the grinding process, preventing the workpiece from overheating and warping. Coolant also improves the surface finish by washing away metal chips and debris. In rough grinding, coolant is less critical, but it can still be used to extend the life of the grinding wheel.
Equipment and Tools
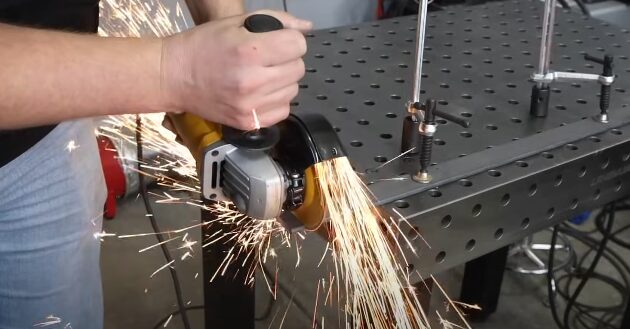
The type of grinding machine you use depends on the job at hand. Rough grinding often involves machines like bench grinders or angle grinders. These machines are designed for heavy-duty material removal and can handle the aggressive nature of rough grinding. Precision grinding, on the other hand, requires more specialized machines like cylindrical grinders, surface grinders, or centerless grinders. These machines offer the accuracy and control needed for precise finishes.
Grinding wheels are the heart of the grinding process. In rough grinding, you’ll typically use wheels with coarser abrasives to remove material quickly. These wheels are designed to withstand the rigors of heavy-duty grinding. For precision grinding, you’ll need wheels with finer abrasives to achieve the desired surface finish. The size of the grinding wheel also matters. Larger wheels are often used for rough grinding, while smaller wheels are more common in precision grinding.
Surface Finish Requirements
Surface roughness is a crucial factor in precision grinding. It’s measured using standards like Ra (average roughness) or Rz (maximum peak-to-valley height). These measurements determine the level of smoothness on the workpiece’s surface. Precision grinding aims for very low surface roughness values to achieve the desired functionality and performance.
Industries that demand extremely precise surface finishes include aerospace, automotive, medical device manufacturing, and semiconductor production. These industries require components with smooth surfaces to ensure optimal performance, durability, and reliability. For example, engine components in the automotive industry need smooth surfaces to reduce friction and improve efficiency.
Quality and Inspection
Quality control is crucial in precision grinding to ensure that your parts meet the required standards. You need to implement processes to monitor every step of the grinding process. This includes checking the grinding machine’s settings, inspecting the grinding wheel, and measuring the workpiece at regular intervals. By doing this, you can identify any issues early on and take corrective action.
To verify dimensional accuracy and surface finish, you need the right inspection tools and techniques. You can use tools like calipers, micrometers, and height gauges to measure dimensions. To assess surface finish, you can use surface roughness testers. Additionally, you can use optical inspection methods like microscopes to examine the surface for defects.
Cost and Efficiency
Cost per part is a critical consideration in both rough and precision grinding. While rough grinding is generally less expensive due to higher material removal rates, you need to balance this with the cost of subsequent finishing processes. Precision grinding, on the other hand, can be more expensive due to the time and equipment involved. However, the higher cost is often justified by the improved part quality and reduced scrap rates.
Rough grinding can significantly impact production timelines as it quickly removes material. This can shorten overall production time. Precision grinding, while slower, is essential for achieving the desired accuracy and finish. It might extend production time, but it’s a necessary step for high-quality parts. Balancing speed and accuracy is key to optimizing production efficiency and cost-effectiveness.
Skill and Expertise
Operator skill and experience play a crucial role in both rough and precision grinding. While rough grinding may seem less demanding, operators still need to understand machine operation, wheel selection, and safety procedures. Precision grinding requires a higher level of skill and training. Operators need to have a deep understanding of grinding parameters, workpiece materials, and quality control methods.
Automation and technology are transforming the grinding industry. In rough grinding, automated systems can handle repetitive tasks and improve efficiency. Precision grinding has also benefited from advancements in technology, with CNC machines and robotic systems capable of performing complex grinding operations with high accuracy. These technologies not only improve productivity but also enhance part quality and consistency.
Conclusion
Understanding the nuances between rough and precision grinding is essential for optimizing manufacturing processes. By carefully selecting the appropriate method, equipment, and parameters, you can achieve optimal results in terms of efficiency, cost, and part quality.