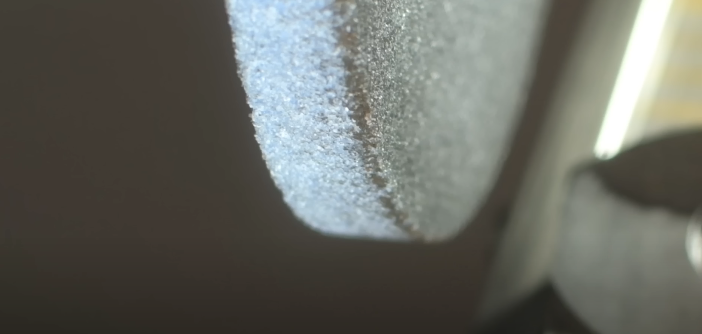
Understanding how a grinding wheel wears is crucial for maintaining efficient and safe grinding operations. Wheel wear impacts performance, safety, and the overall lifespan of the grinding process. Several factors contribute to wheel wear, and recognizing these factors is essential for optimizing grinding outcomes. And here’s exactly what happens when a grinding wheel wears.
Surface Degradation
As you use your grinding wheel, the abrasive particles on its surface gradually diminish. Imagine the wheel as a brush with bristles. As you brush, the bristles become shorter. Similarly, the abrasive grains on your grinding wheel shorten with each use. This loss of abrasive material affects the wheel’s performance.
Alongside the loss of abrasive material, the wheel’s surface also becomes rougher. Picture a brand new brush with soft bristles. Over time, the bristles fray, and the brush becomes less smooth. Your grinding wheel undergoes a similar process. As the abrasive grains wear down, the wheel’s surface develops tiny irregularities, leading to increased surface roughness.
Change in Wheel Shape and Profile
As a grinding wheel is used, its diameter gradually decreases. Imagine a pencil that gets shorter with each sharpening; the same principle applies to a grinding wheel. This reduction in diameter affects the wheel’s contact area with the workpiece, influencing factors like material removal rate, surface finish, and grinding forces.
Beyond diameter reduction, a worn grinding wheel can also suffer from a loss of form. The ideal shape of a grinding wheel is crucial for maintaining consistent contact and performance. Over time, the wheel can become out of round, develop concavity, or exhibit other irregularities. These distortions impact the grinding process, leading to uneven material removal, vibration, and potential damage to both the workpiece and the wheel itself.
Performance Degradation
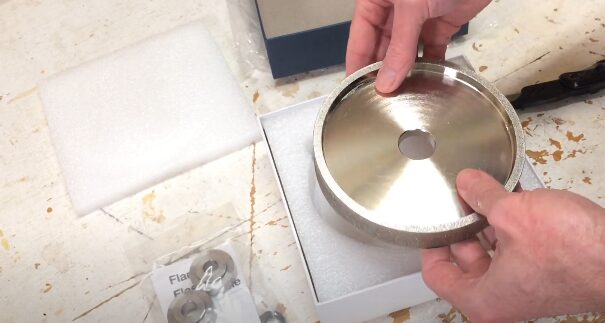
As a grinding wheel wears, you’ll notice a significant decline in its material removal rate. Imagine trying to cut wood with a dull saw; it requires more effort and time to achieve the desired result. Similarly, a worn grinding wheel with fewer sharp abrasive grains removes material at a slower pace. This translates to longer grinding times, reduced productivity, and increased operational costs.
In addition to slower material removal, a worn grinding wheel produces a poorer surface finish. The degradation of the wheel’s surface leads to increased roughness and inconsistency in the finish. Picture sanding with sandpaper that has lost its grit; the surface becomes uneven and lacks smoothness. A subpar surface finish might necessitate additional finishing operations, further impacting overall production efficiency and part quality.
Increase in Heat Generation
Grinding is inherently a process that generates heat due to the friction between the workpiece and the grinding wheel. However, a worn wheel exacerbates this heat generation. As the abrasive grains become duller and the wheel’s surface degrades, more energy is converted into heat rather than productive work. This increased friction leads to a significant rise in temperatures within the grinding zone.
Beyond the intensified heat generation, a worn wheel also struggles to dissipate heat effectively. The wheel’s structure, designed for optimal heat transfer, becomes compromised as it wears. This reduced heat dissipation capacity allows temperatures to climb rapidly, creating a dangerous environment. Excessive heat can lead to thermal damage to the workpiece, such as burning or cracking, and can also accelerate the wear of the grinding wheel itself, shortening its lifespan.
Vibrations and Noises
A worn grinding wheel can significantly increase vibrations during operation. Imagine a car tire with uneven wear; it causes the vehicle to shake. Similarly, a worn grinding wheel, especially one that’s out of round, can induce vibrations that affect workpiece accuracy, surface finish, and operator comfort. Prolonged exposure to excessive vibrations can also damage the grinding machine itself.
In addition to increased vibrations, a worn wheel often produces unusual noises. A healthy wheel typically generates a consistent grinding sound. However, as the wheel deteriorates, you might hear high-pitched squeals, chattering, or even a harsh, grating sound. These noises are clear indicators of wheel wear and should prompt immediate inspection. Ignoring these auditory cues can lead to catastrophic wheel failure.
Effect on Coolant Effectiveness
Coolant plays a vital role in managing the heat generated during grinding. However, a worn grinding wheel can disrupt the coolant’s effectiveness. The wheel’s surface can become clogged with debris, hindering the coolant’s ability to reach the grinding zone. This reduced coolant flow impacts heat dissipation, leading to higher temperatures in the grinding area.
Inadequate cooling due to a worn wheel poses several risks. Excessive heat can cause the workpiece to warp or develop microcracks, compromising its integrity. Additionally, the grinding wheel itself can overheat, leading to premature wear, cracking, or even catastrophic failure.
Safety Considerations
A worn grinding wheel poses significant safety risks. As the wheel deteriorates, its structural integrity weakens. This increases the chance of the wheel breaking apart or disintegrating during operation. Wheel fragments can fly off at high speeds, potentially injuring operators or bystanders.
To protect yourself and others, it’s crucial to inspect your grinding wheels regularly for signs of wear. Worn-out wheels can cause uncontrolled grinding, leading to kickbacks, where the workpiece is violently ejected from the machine. This can result in serious injuries. Additionally, excessive vibration from a worn wheel can strain the machine and increase the risk of equipment failure. Prioritizing wheel maintenance and replacement is essential for a safe grinding environment.
Comparison with Manufacturer Specifications
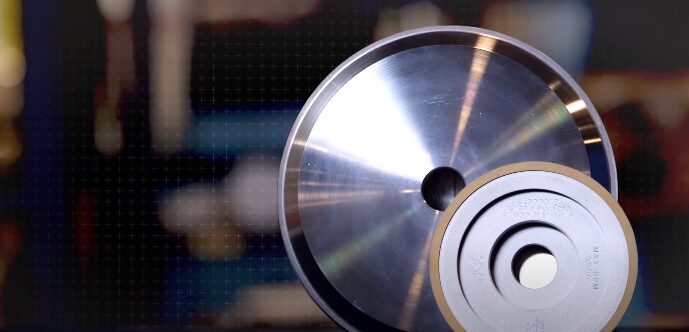
To effectively manage grinding wheel wear, it’s essential to refer to the manufacturer’s guidelines. Each grinding wheel has a recommended lifespan based on its specifications and intended use. Regularly compare your wheel’s condition to these guidelines to determine if it’s nearing the end of its useful life.
Many manufacturers incorporate wear indicators into their grinding wheels. These indicators, often visual cues like color changes or markings, help you assess the wheel’s wear level. By monitoring these indicators, you can proactively plan for wheel replacement and avoid unexpected failures.
Conclusion
To get the maximum grinding performance, make the process more secure, and extend the lifecycle of the equipment regular inspection is required. The wheel should be examined for wear and tear, guided by the manufacturer, and correct maintenances should be followed which is the most critical step to not losing money due to technical problems.