Grinding wheels are indispensable tools in various industries, facilitating the shaping and finishing of workpieces with precision and efficiency. However, despite their importance, they are susceptible to wear and degradation over time, leading to issues such as surface burning during the grinding process. In this article, we delve into effective maintenance strategies to prevent burn-related problems associated with grinding wheels.
Understanding the Importance of Grinding Wheel Maintenance
Grinding wheels play a critical role in achieving desired surface finishes and dimensional accuracies in machining operations. They are subjected to high stresses and temperatures during grinding, which can cause wear and deterioration if not properly maintained. Neglecting grinding wheel maintenance not only compromises workpiece quality but also poses safety risks and increases production costs due to frequent replacements.
Identifying the Causes of Surface Burning
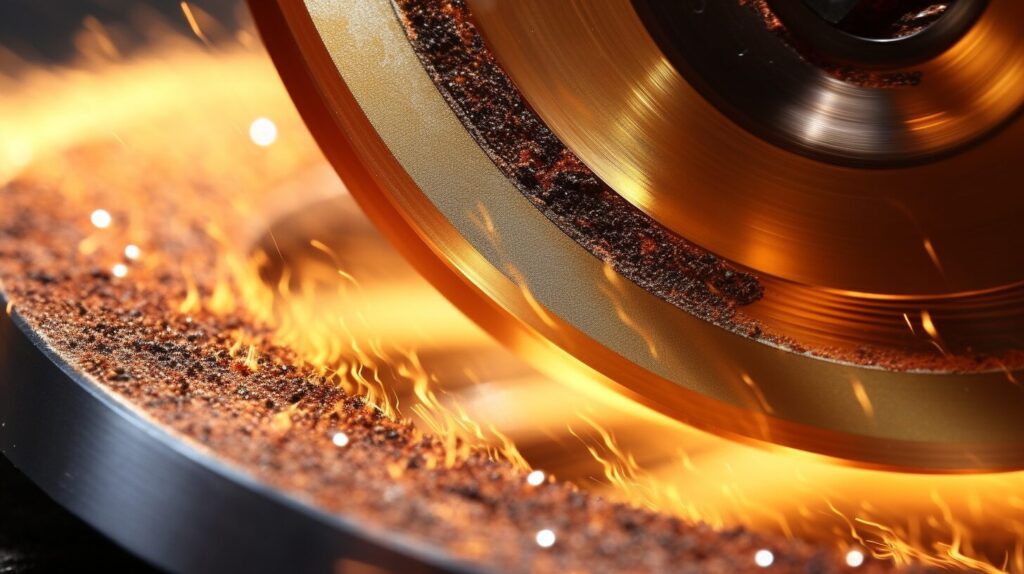
Surface burning, characterized by discoloration and thermal damage on workpiece surfaces, often occurs towards the end of the grinding process. This phenomenon can be attributed to several factors, with grinding wheel condition being a primary concern. As grinding wheels wear down or become clogged with debris, their cutting efficiency decreases, leading to higher grinding forces and heat generation. Additionally, inadequate heat dissipation and self-sharpening properties exacerbate heat accumulation, resulting in surface burning.
Regular Dressing of Grinding Wheels
One of the fundamental maintenance practices for grinding wheels is regular dressing, which involves removing dulled abrasive grains and restoring the wheel’s geometry. By maintaining sharp cutting edges and an open grain structure, dressed grinding wheels exhibit improved cutting performance and heat dissipation capabilities. Operators should monitor the wear pattern of grinding wheels and dress them accordingly to prevent excessive heat buildup and surface burning.
Selecting Optimal Grinding Wheel Materials
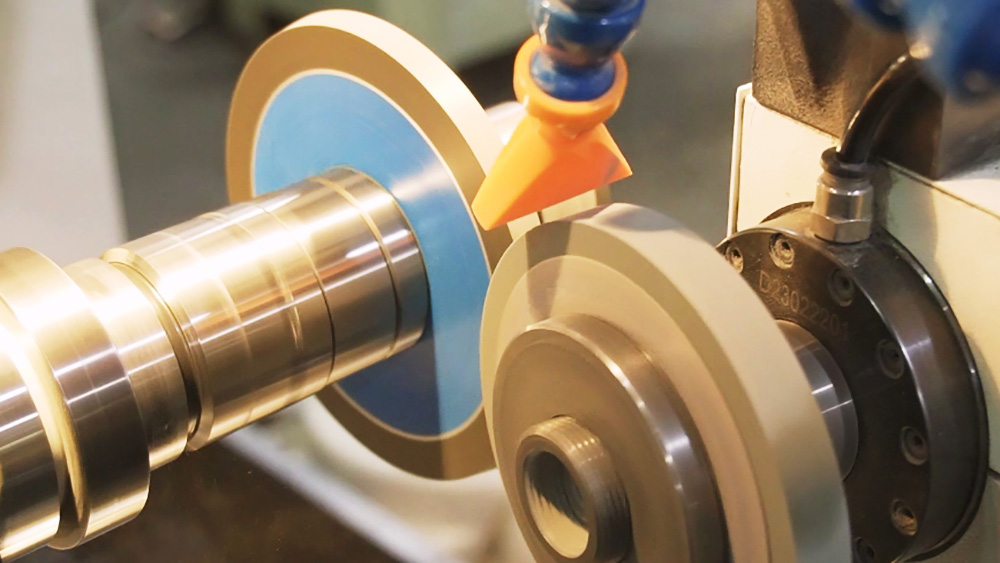
The choice of grinding wheel materials significantly influences its performance and longevity. When selecting grinding wheels, factors such as abrasive type, bond strength, and porosity should be considered to ensure compatibility with specific machining applications. For example, vitrified bond wheels are preferred for high-speed grinding operations due to their excellent heat resistance and abrasive retention properties. By choosing grinding wheels tailored to the application requirements, operators can mitigate the risk of surface burning and enhance overall process efficiency.
Enhancing Heat Dissipation and Self-Sharpening
Effective heat dissipation is crucial for preventing surface burning during grinding operations. Grinding wheels with enhanced thermal conductivity and self-sharpening characteristics offer superior heat dissipation and cutting efficiency, reducing the likelihood of thermal damage to workpieces. Furthermore, optimizing coolant delivery systems and ensuring adequate lubrication between the grinding wheel and workpiece interface contribute to efficient heat removal and minimized surface burning.
Implementing Comprehensive Process Management
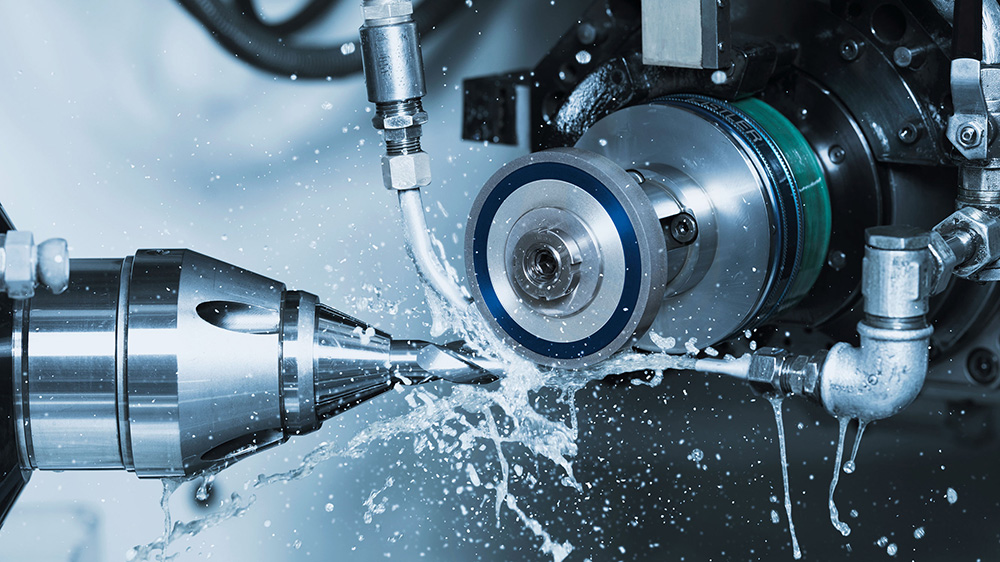
In addition to specific maintenance practices, comprehensive process management plays a vital role in preventing surface burning and maximizing grinding performance. This includes monitoring and controlling grinding parameters such as wheel speed, feed rate, and depth of cut to maintain optimal cutting conditions and minimize heat generation. Furthermore, regular inspection of machine tools and workpiece setups helps identify potential sources of vibration and instability that may contribute to surface burning.
Conclusion
Grinding wheel maintenance is paramount for preventing surface burning and ensuring consistent workpiece quality in machining operations. By implementing proactive strategies such as regular dressing, selecting optimal grinding wheel materials, and optimizing process parameters, operators can minimize the risk of thermal damage and achieve superior grinding performance. With proper maintenance and attention to detail, grinding wheels can effectively meet the demands of modern manufacturing processes while ensuring efficient and cost-effective production.