In industrial manufacturing, the efficient use of abrasive wheels is paramount for enhancing productivity and reducing costs. Abrasive wheels, commonly known as grinding wheels, play a crucial role in various machining processes, impacting the quality and efficiency of the final products. This article explores essential strategies to maximize efficiency in abrasive wheel grinding, ensuring success in manufacturing operations.
Understanding Abrasive Wheels
In industrial manufacturing, the efficient use of abrasive wheels is paramount for enhancing productivity and reducing costs. Abrasive wheels, commonly known as grinding wheels, play a crucial role in various machining processes, impacting the quality and efficiency of the final products. This article explores essential strategies to maximize efficiency in abrasive wheel grinding, ensuring success in manufacturing operations.
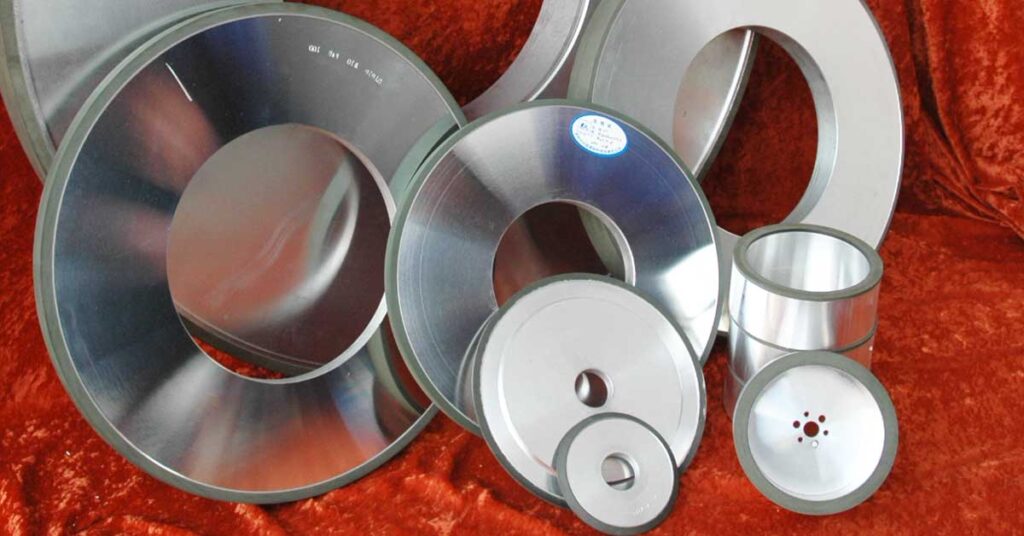
Selecting the Right Abrasive Wheel
Choosing the appropriate abrasive wheel is the first step towards efficient grinding. Factors such as wheel material, grit size, hardness, and bond type must be carefully considered based on the material properties, desired finish, and precision requirements of the workpiece. For example, silicon carbide wheels are ideal for grinding non-ferrous metals, while aluminum oxide wheels are suitable for ferrous metals. Selecting the right wheel ensures optimal performance and longevity.
Optimizing Grinding Parameters
Adjusting grinding parameters is critical for achieving efficient and effective results. Parameters such as wheel speed, feed rate, depth of cut, and coolant usage directly impact grinding performance. Balancing these parameters according to the material being ground and desired outcomes is essential. Increasing wheel speed can enhance productivity, but excessive speeds may lead to wheel wear and overheating. Similarly, optimizing feed rates and depth of cut ensures efficient material removal without compromising surface quality.
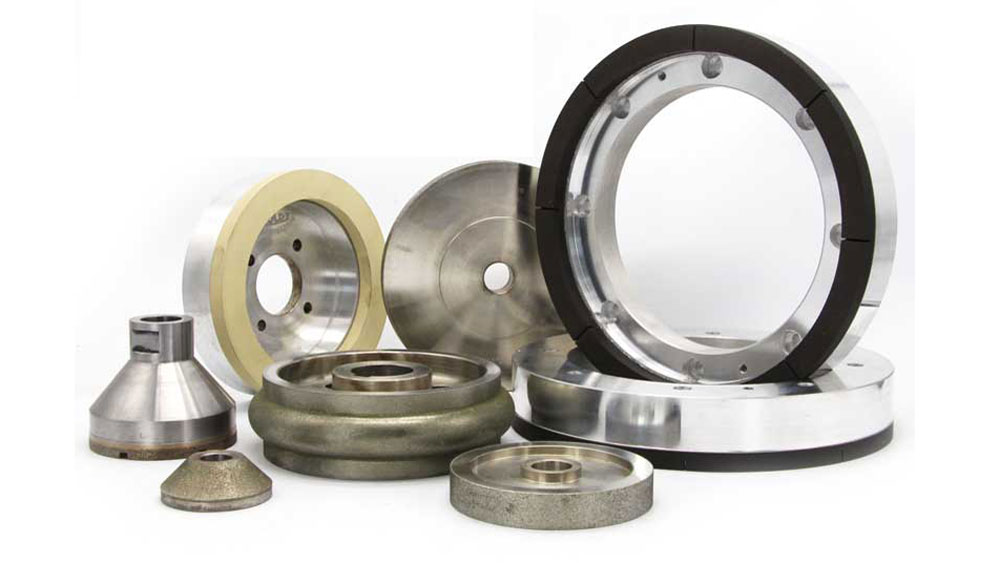
Maintaining Wheel Sharpness and Cleanliness
Maintaining the sharpness and cleanliness of abrasive wheels is crucial for consistent performance. Over time, grinding wheels become dull due to wear and accumulation of swarf (metal particles) and coolant residues. Regular dressing and cleaning of wheels are necessary to remove debris and restore sharpness. Additionally, proper coolant management helps dissipate heat and prevent workpiece overheating, prolonging wheel life and ensuring optimal grinding performance.
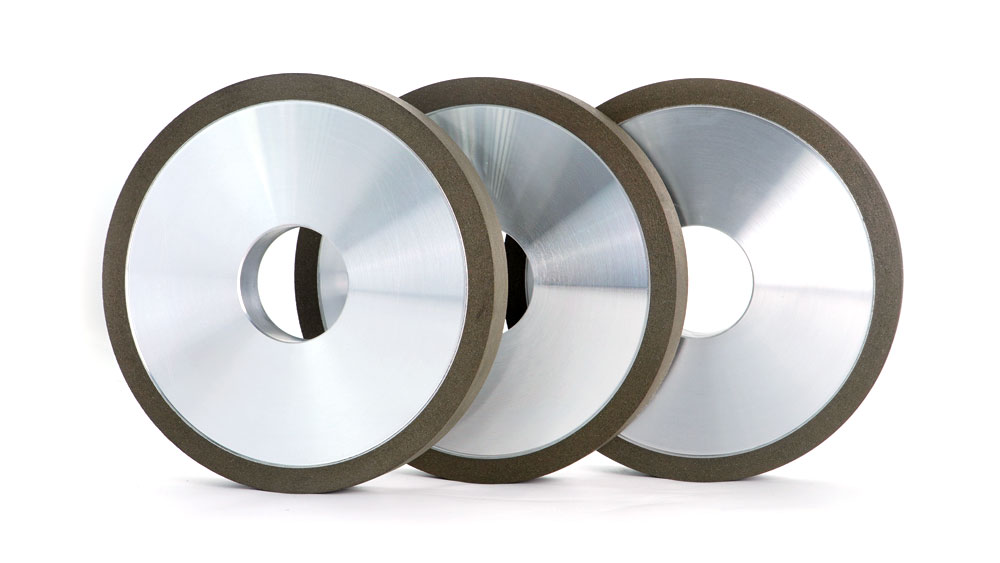
Implementing Advanced Technologies
Advancements in technology have revolutionized abrasive wheel grinding, offering new opportunities for efficiency and precision. Automation, robotics, and computer numerical control (CNC) systems enable precise control of grinding operations, reducing human error and enhancing repeatability. Furthermore, innovative abrasive wheel designs and materials enhance cutting efficiency and surface finish, pushing the boundaries of productivity and quality in grinding applications.
Conclusion
Efficient abrasive wheel grinding is essential for maximizing productivity and achieving success in industrial manufacturing. By understanding abrasive wheel characteristics, selecting the right wheels, optimizing grinding parameters, maintaining wheel sharpness and cleanliness, and leveraging advanced technologies, manufacturers can enhance efficiency, reduce costs, and improve product quality in grinding operations.