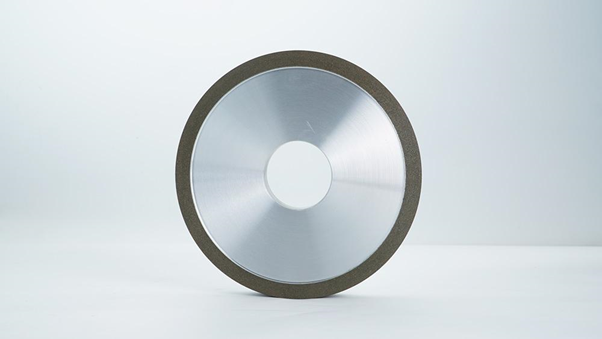
Ever wondered what makes one grinding wheel perfect for a specific job, while another leaves you with a rough finish? It all boils down to the grade of the grinding wheel. The grade refers to how strongly the bond holds the abrasive grains within the wheel. This seemingly simple concept significantly impacts how the wheel performs and ultimately determines the outcome of your grinding project.
TABLE OF CONTENTS
MAKEUP OF A GRINDING WHEEL
THE ABRASIVE MATERIAL
ALUMINUM OXIDE
This versatile material is a popular choice for a wide range of grinding applications. It excels at grinding materials of high tensile strength, such as stainless steel and tool steels. Aluminum oxide comes in various grades, allowing you to tailor the cutting power to your specific needs.
SILICON CARBIDE
Known for its exceptional hardness, silicon carbide is ideal for tackling tough materials like carbide and ceramics. It breaks down quickly, exposing fresh sharp edges continuously, making it a great choice for fast and aggressive grinding.
CUBIC BORON NITRIDE (CBN)
This superabrasive boasts incredible hardness, even surpassing silicon carbide. CBN is perfect for grinding high-hardness materials like hardened steel and tool steels while maintaining a sharp cutting edge and long wheel life.
DIAMOND
The undisputed king of abrasives, diamond offers unparalleled hardness and cutting ability. It’s ideal for grinding extremely hard and abrasive materials like concrete, stone, and even other superabrasives.
BONDING MATERIAL
The bonding material acts like the glue in a grinding wheel, holding the abrasive grains together and ensuring they don’t come loose during grinding. The type of bond you choose will influence the grinding performance, wheel life, and the overall finish achieved. Here are some of the most common bonding materials:
- Vitrified Bond: Made from glass, vitrified bonds are incredibly strong and durable. They excel in high-pressure grinding applications and are often used with harder abrasives like aluminum oxide and silicon carbide.
- Resin Bond: Offering more flexibility than vitrified bonds, resin bonds are a popular choice for finer grinding and finishing work. They allow the abrasive grains to fracture more easily, exposing fresh cutting edges and resulting in a smoother finish.
- Metal Bond: Metal bonds provide the ultimate strength and are typically used for grinding extremely hard materials or in high-pressure applications. They hold the abrasive grains very tightly, resulting in a slow wear rate but a less aggressive grinding action.
- Electroplated Bond: In this method, the abrasive grains are bonded to a metal base using an electroplating process. This creates a very thin and precise grinding wheel that’s ideal for delicate applications and achieving ultra-fine finishes.
- Rubber Bond: Rubber bonds offer superior flexibility and shock absorption, making them a good choice for grinding on uneven surfaces or for applications where vibration is a concern. They are often used with softer abrasive materials for light grinding or deburring.
TYPES OF BONDING AGENTS FOR GRINDING WHEELS
The bond you choose is vital in how your grinding wheel performs. It dictates factors like wheel life, cutting aggressiveness, and the final finish achieved on your workpiece. Let’s delve into the most common bonding materials and their ideal applications:
VITRIFIED BOND
This classic bond, made from glass, is renowned for its strength and durability. It excels in high-pressure grinding situations and is often paired with conventional abrasives like aluminum oxide and silicon carbide. Vitrified bonds hold the abrasive grains firmly, allowing them to wear down gradually for a long wheel life. However, due to their slower rate of abrasive grain release, they can be less forgiving for delicate work.
RESINOID BOND
Offering more flexibility compared to vitrified bonds, resin bonds are a popular choice for achieving finer finishes. They are well-suited for both conventional and super abrasive wheels. The bond allows the abrasive grains to fracture more readily, constantly exposing fresh cutting edges. This translates to a smoother grinding action and a superior final surface on your workpiece. However, resin bonds may not be ideal for heavy-duty grinding due to their slightly less robust structure.
METAL BOND
When you need maximum strength to tackle extremely hard materials, metal bonds come into play. They are typically used with super abrasive wheels like diamond and CBN. Metal bonds hold the abrasive grains very tightly, resulting in a slow wear rate but a less aggressive grinding action. This makes them ideal for situations where precise control and long wheel life are paramount.
ELECTROPLATED BOND
This specialized bonding method uses an electroplating process to attach abrasive grains to a metal base. This creates a very thin and precise grinding wheel, perfect for delicate applications and achieving ultra-fine finishes. Electroplated bonds are most commonly found in superabrasive wheels.
BRAZED BOND
Similar to metal bonds, brazed bonds offer superior strength for grinding very hard materials. Here, the abrasive grains are joined to a metal base using a high-temperature brazing process. Brazed bonds are another option for super abrasive wheels, particularly when a combination of strength and good heat tolerance is required.
RUBBER BOND
Similar to metal bonds, brazed bonds offer superior strength for grinding very hard materials. Here, the abrasive grains are joined to a metal base using a high-temperature brazing process. Brazed bonds are another option for super abrasive wheels, particularly when a combination of strength and good heat tolerance is required.
COMPOSITION OF THE GRINDING WHEEL
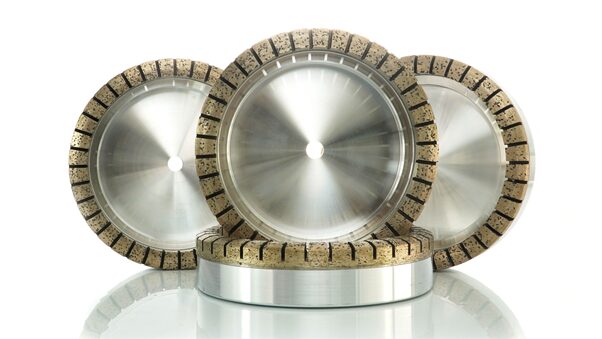
When it comes to the grinding wheel grade, its composition needs to be examined to get a better understanding of it. Two essential components are abrasive material and bonding material that makes a grinding wheel: the abrasive is the material that cuts, and the bond is the material that holds the abrasive together. The abrasives, namely aluminium oxide, which is the non-metallic material, or silicon carbide, the metallic type, are those very hard but sharp particles that do the actual grinding. The kind of abrasive will decide what materials it is good at grinding. For one, aluminium oxide is lascivious to steel, so one can easily disassemble it, while silicon carbide can process even the harder ones like ceramics.
The bonding material is the one that works as the adhesive. It is what binds the abrasive particles together. The most common bonding ways are vitrified bonds (glass) and resin bonds (synthetic resins) and metal bonds (metallic elements). The bond’s selection will determine whether the resultant wheel becomes stronger or not as well as if it withstands heat/pressure during grinding better or not.
ABRASIVE GRAIN SIZE
The grain size of a grinding wheel refers to the average diameter of the abrasive grains on its surface. A larger grain size means coarser grit, while a smaller grain size indicates finer grit. Coarse-grit wheels are excellent for aggressive stock removal. They can quickly remove material, but they produce a rougher finish. These wheels are ideal for shaping and roughing out workpieces.
Fine-grit wheels, on the other hand, are designed for finishing operations. They produce a smoother surface finish but remove material at a slower rate. These wheels are perfect for achieving precise dimensions and desired surface quality.
It’s important to match the grain size to your application. If you’re working with hard materials or need to remove a lot of material quickly, a coarser grit wheel is suitable. For delicate work or achieving a fine finish, a finer grit wheel is the way to go.
WHEEL HARDNESS & GRADE
Now, let’s get back to the main topic – grade. This is designated by a letter code ranging from A to Z, with softer grades denoted by letters closer to the beginning of the alphabet and harder grades towards the end. Here’s the breakdown:
- Softer Grades (A-H): These wheels have a weaker bond, allowing the abrasive grains to wear away more easily. This is ideal for grinding hard materials like tool steel, where a softer wheel conforms to the workpiece and prevents glazing (when the wheel surface clogs with metal particles).
- Harder Grades (I-Z): With a stronger bond holding the grains firmly in place, these wheels resist wear and tear better. They’re perfect for softer materials like aluminum or for applications requiring a high stock removal rate.
STRUCTURE OF THE WHEEL
The structure of a grinding wheel, often referred to as its density or openness, is another crucial factor influencing the wheel’s grade and overall performance. Imagine the grinding wheel as a sponge – more holes (open structure) allow for better water flow and chip removal, while fewer holes (closed structure) offer increased support for the abrasive grains.
This seemingly simple concept has significant ramifications. An open structure wheel features more void spaces between the abrasive grains. This translates to better chip removal, preventing the wheel from clogging during grinding. It also allows for improved coolant flow, which is essential for reducing grinding temperatures and preventing workpiece burns. However, the downside of an open structure is that it offers less support for the abrasive grains. This can lead to faster grain breakdown, particularly when grinding harder materials or applying heavy pressure.
On the other hand, a closed structure wheel has fewer voids between the abrasive grains. This provides a denser structure with increased support for the abrasive grains. This makes it ideal for heavy-duty grinding applications where aggressive cutting action is required. However, a closed structure can hinder chip evacuation and coolant flow. This can lead to heat buildup, reduced grinding efficiency, and potential workpiece damage.
Understanding how the bond type interacts with the abrasive material and structure is essential for selecting the right wheel for the job. A soft, resinoid bond paired with a closed structure creates a softer grade wheel that excels at achieving a smooth finish. Conversely, a hard, vitrified bond with an open structure results in a harder grade wheel that prioritizes faster material removal and good dimensional control.
APPLICATION AND USE
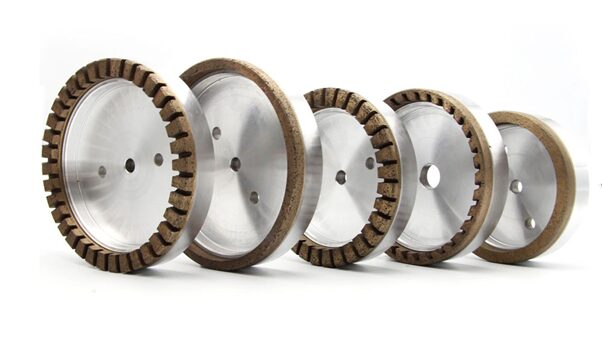
Let’s break down how to select the right wheel for your task.
REGULAR GRINDING WHEELS
Vitrified bond wheels are the most versatile type you’ll find. They handle a wide range of materials, from ferrous to non-ferrous metals. For roughing up tough materials, look for a coarse-grit, open-structure vitrified wheel. This combination excels at aggressive material removal. On the other hand, if you’re aiming for a fine finish on softer metals, opt for a fine-grit, dense structure vitrified wheel.
Resinoid bond wheels are known for their flexibility. They’re perfect for high-speed grinding, cutting off materials, and snagging. You’ll often find them used in industries like automotive and aerospace. Rubber bond wheels are soft and pliable. This makes them ideal for lighter tasks like deburring and finishing on soft materials such as aluminum or plastics.
Ceramic bond wheels are built for toughness. They can withstand high temperatures and wear exceptionally well, making them perfect for grinding hard materials like stainless steel, titanium, and superalloys. These wheels are commonly found in aerospace and manufacturing settings.
SUPERABRASIVE GRINDING WHEELS
Diamond and CBN wheels are the heavy hitters in the grinding world. Renowned for their exceptional hardness, diamond wheels are your go-to for precision tasks like grinding, sharpening, and refining hard materials such as ceramics, carbides, and hardened steel. They’re indispensable in tool and die-making. If you’re working with even tougher materials like hardened steels, cast iron, or superalloys, CBN (Cubic Boron Nitride) wheels are your best bet.
They can handle extreme temperatures and last longer than most other options, making them a top choice for demanding applications. By carefully considering the material you’re working with, the desired finish, and the specific grinding operation, you can select the appropriate grinding wheel grade and bond to achieve optimal results.
MANUFACTURER SPECIFICATIONS
Selecting the appropriate grade of grinding wheel doesn’t have to be a guessing game. Grinding wheel manufacturers establish industry standards and guidelines to assist you in making informed decisions. These specifications often encompass a wealth of information, including:
- Recommended Applications: Manufacturers typically categorize their wheels based on suitable applications. This can range from general-purpose grinding to specific material recommendations (e.g., wheels for grinding stainless steel or cast iron). By identifying the material you’ll be working with, you can narrow down your search to wheels with compatible grade ranges.
- Grade Charts: Many manufacturers provide handy grade charts that visually represent the relationship between abrasive material, bond type, structure, and the resulting grade. These charts can be invaluable tools for understanding how different factors combine to influence the wheel’s performance.
- Safety Data Sheets (SDS): Don’t underestimate the importance of safety data sheets! These documents not only provide crucial safety information but often include details on the recommended operating speeds and grinding pressures for specific wheel grades. Following these guidelines ensures optimal performance and safe operation of the grinding wheel.
While standardized grinding wheels cater to most applications, there are situations where a custom solution might be necessary. Some manufacturers offer the option to customize the grade of a grinding wheel. This can involve adjustments to the abrasive material, bond type, or structure to achieve a specific performance characteristic.
For example, if you require a grinding wheel with a softer grade than what’s commercially available, a manufacturer might be able to adjust the bond formulation to achieve the desired result. Customization can be particularly beneficial for high-volume production environments or when working with unique materials or grinding processes.
TESTING AND QUALITY CONTROL
Throughout the manufacturing process, grinding wheels undergo rigorous testing methods to verify their grade and overall performance. These tests evaluate factors like:
- Wheel Strength: Testing ensures the wheel can withstand the intended grinding forces without fracturing or breaking apart.
- Balance: An unbalanced wheel can cause vibrations during grinding, leading to uneven finishes and potential safety hazards. Testing guarantees the wheel is properly balanced for smooth operation.
- Grain Retention: Tests assess how well the bond holds onto the abrasive grains. This directly relates to the wheel’s grade and grinding efficiency.
Quality control is paramount in the grinding wheel industry. These meticulous testing procedures ensure that each wheel, regardless of batch, meets the specified grade and performance standards. This consistency translates to predictable grinding results and allows you to rely on the wheel’s behavior from one project to the next.
By understanding the role of manufacturer specifications and the importance of testing and quality control, you can feel confident in selecting a grinding wheel with the appropriate grade for your specific grinding application. Remember, the right wheel can make all the difference in achieving efficient grinding, a high-quality finish, and overall success in your workshop