Brief Introduction of conventional grinding wheels
Silicon carbide and aluminum oxide grinding wheels are the main conventional grinding wheels, they can be a vitrified bond, resin bond and rubber bond. And bench grinder wheel is one of the most popular grinding wheels. And there are also many other types of grinding wheels made of different abrasive grains, if you like to know, follow Mrbrianzhao.
Hello everyone, I’m Mrbrianzhao, who will constantly share with you abrasive knowledge and offer you the best solution for your grinding production, First, let’s talk about the bench grinder wheel.
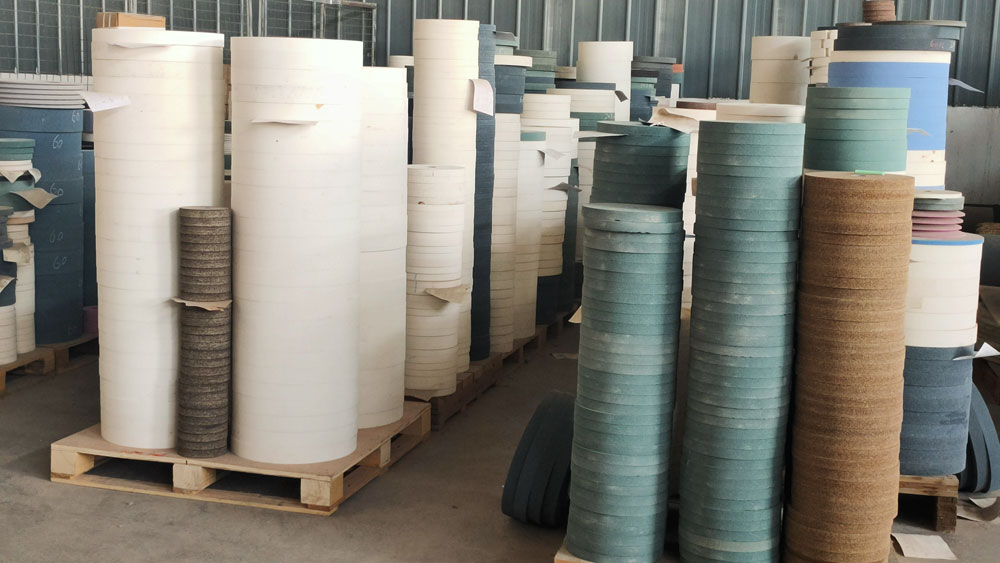
conventional grinding wheels' Application
Bench Grinder Wheel
One of the most popular conventional grinding wheels is bench grinder wheel, This bench grinder wheel was designed to fit most stationary bench grinding machines for high speed steel sharpening and deburring. It features premium white aluminum oxide with a vitrified bond. As this abrasive grinds down with wear, it produces a consistent and fresh grinding surface for balanced work.
Whether sharpening your metal lathe turning tools, lawnmower blades or other HSS tools – this grinding wheel stone will get the job done with high precision results. We aim to ensure that your grinding results are top-notch and hassle free with these ultra-hard, durable, long-lasting, precision accessories.
(It is not recommended that you grind wood, plastic or any other non-metallic material on a bench or pedestal grinder.)
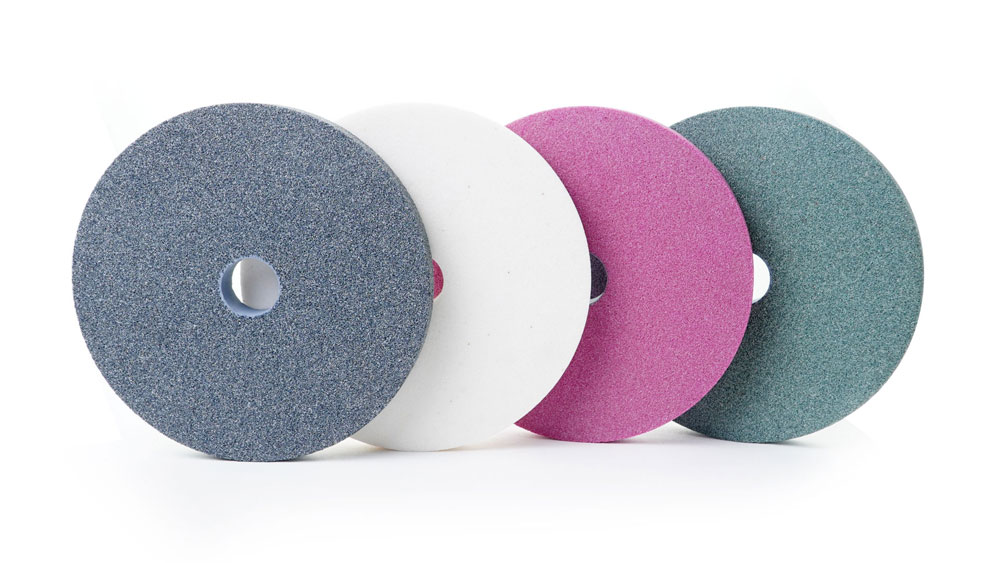
Features of bench grinder wheel
Different Abrasive Grains of Conventional Grinding Wheels
Aluminum oxide:
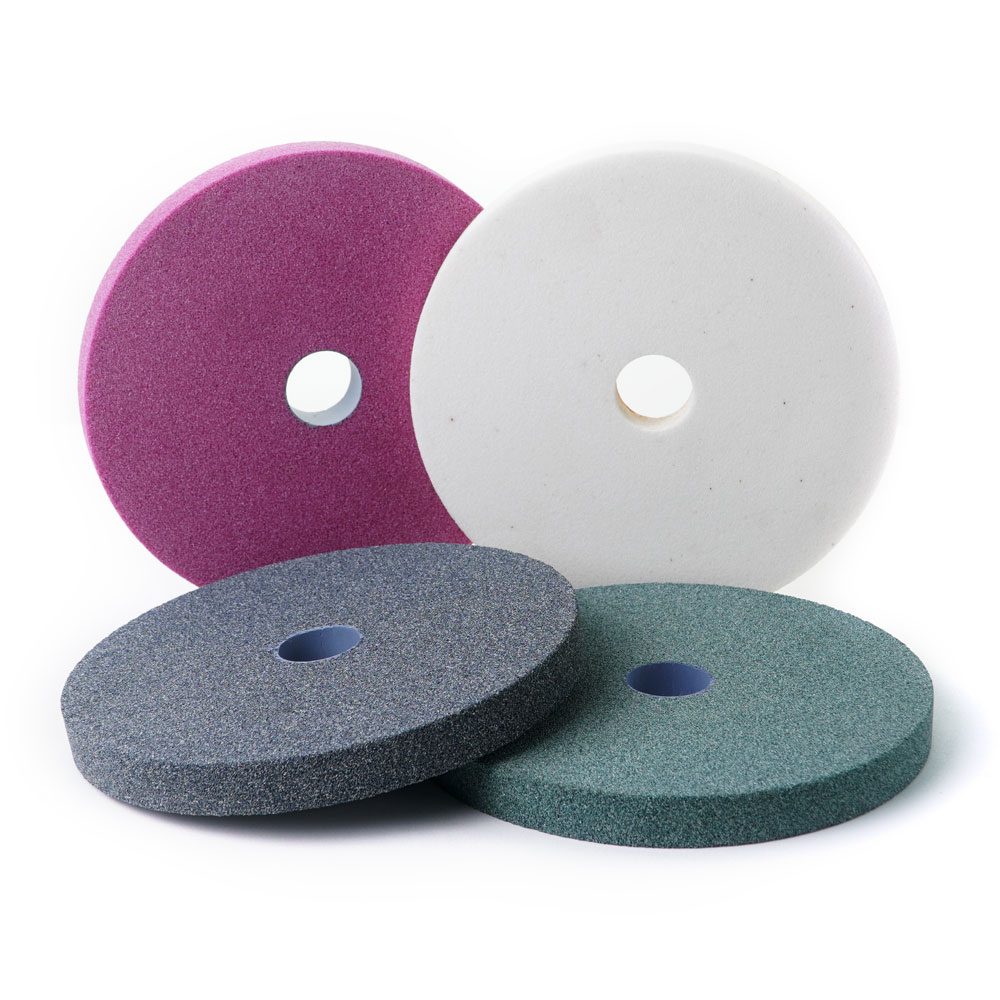
Aluminum oxide is very popular and main material used for conventional grinding wheels, An aluminum oxide grain is ideal for steel, iron and other metals. Although it is hard and durable and provides a sharp, fast initial cut, the grain dulls over time and lacks the cut-rate and potential longevity of some other grains. Aluminum oxide provides exceptional value and cost-effectiveness while still offering the excellent quality and consistent performance necessary in a grinding wheel.
Aluminum Oxide is manufactured in varying qualities. Generally recommended for grinding materials of high tensile strength, such as stainless steel and tool steels but it can also be used on some high tensile Aluminum and bronze alloys. Aluminum Oxide also called corundum, material includes Brown aluminum oxide (A), White aluminum oxide (WA), Pink aluminum oxide (PA), Single crystal aluminum oxide (SA) and Micro crystal aluminum oxide (MA).
Silicon carbide:
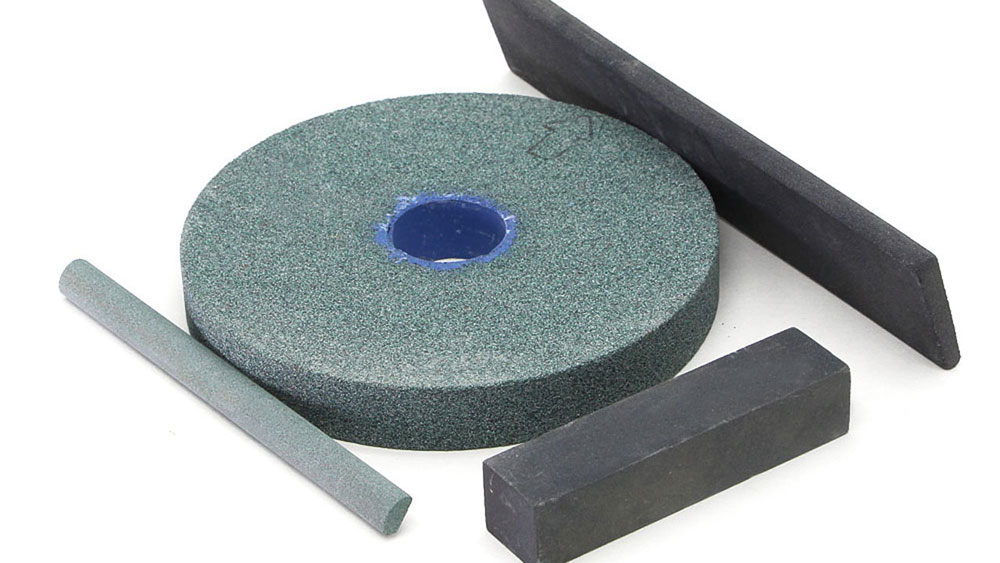
Silicon carbide another main material of conventional grinding wheels which is an extremely hard grain that is very sharp and fast cutting but friable, not as tough as other grains. Harder than standard aluminum oxide with a very sharp abrasive grain. It is a versatile material, recommended for grinding relatively soft metals such as Aluminum or cast iron but can also be used on extremely hard materials such as cemented carbide.
Harder than standard aluminum oxide with a very sharp abrasive grain. It is a versatile material, recommended for grinding relatively soft metals such as aluminum or cast iron but can also be used on extremely hard materials such as cemented carbide.
A wheel made from a blend of silicon carbide and aluminum oxide provides ideal grinding for aluminum and other soft alloys. These grains offer extended life spans and fast, consistent cut rates on aluminum and other soft metals. Silicon Carbide Abrasive Tools are used for brittle and hard carbide, glass, gem, stone grinding, cutting, or super fine grinding. The material includes Black silicon carbide (C), Green silicon carbide (GC) etc.
Aluminum oxide and silicon carbide will be formed into bonded abrasives like Surface Grinding Wheels, Centerless Grinding Wheels, Cylindrical Grinding Wheels, Internal Grinding Wheels, Grinding Discs, Cutting discs, Mounted Points, and Sharpening Stones etc. These grindstones’ bond used can be vitrified, resin or rubber bond. Customized products are also available.
8 Main abrasive grains of conventional grinding wheels
White aluminum Oxide:
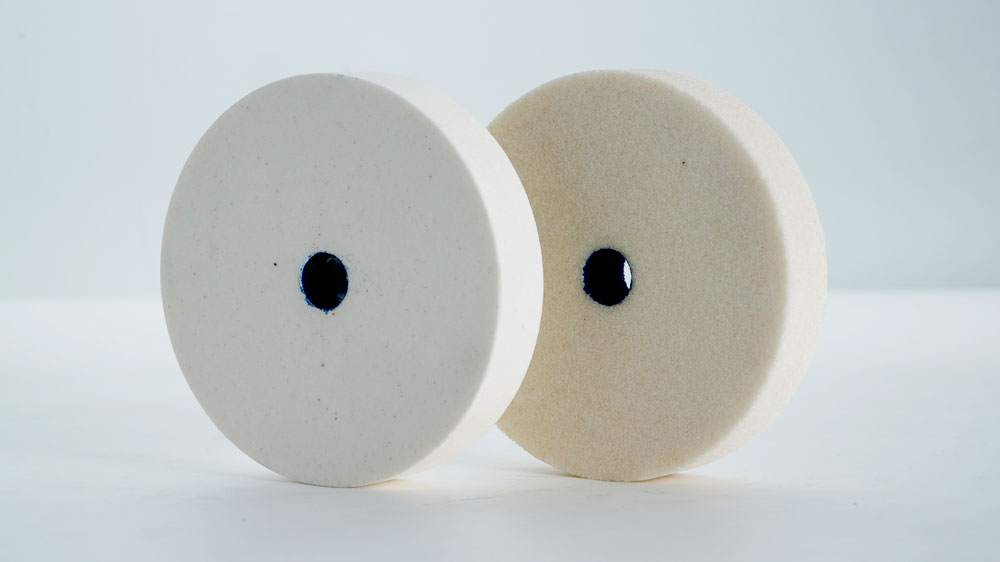
Composition Materials supplies 99.4% pure White Aluminum Oxide abrasive in all standard sizes. One of the most popular conventional grinding wheels. This product is used in a wide variety of industries including automotive, aircraft, medical, dental, cosmetic and flooring.
Obtained from the fusion of calcined alumina in electric arc furnaces, this sharp, fast-cutting, very hard abrasive is effective in media blasting, cleaning, glass etching and surface preparation. In the cosmetics industry, Microdermabrasion Crystals are used for exfoliation creams and skin treatments.
Pink Aluminum Oxide:
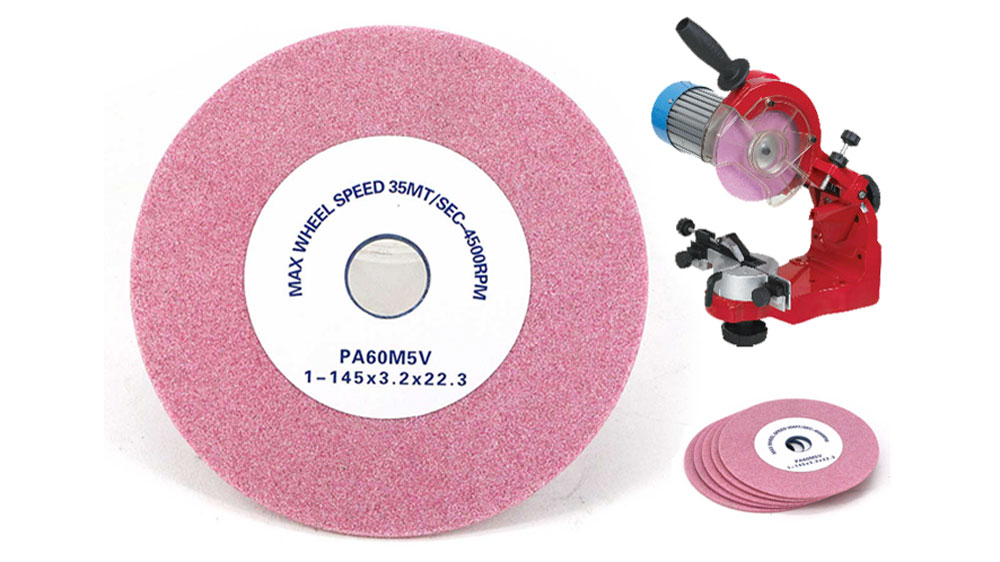
Pink Fused Alumina is produced by adding chromium oxide to high purity aluminum oxide during the fusion process. As a conventional grinding wheels, it is low cost and suitable for most chainsaw users. The amount of chromium oxide added affects the color of the final product, as well as the toughness of the grain. With increased additions of chromium oxide, the toughness of the grain increases.
Pink Aluminum Oxide, which is highly demanded among the clients due to its toughness. This product is formulated using high-grade ingredients that are sourced from the authentic vendors of the market. We process this product by fusing chromium into the atoms of aluminum oxide. Our offered Pink Aluminum Oxide is advised to be used for high stock removals during rough honing.
Brown Aluminum Oxide:
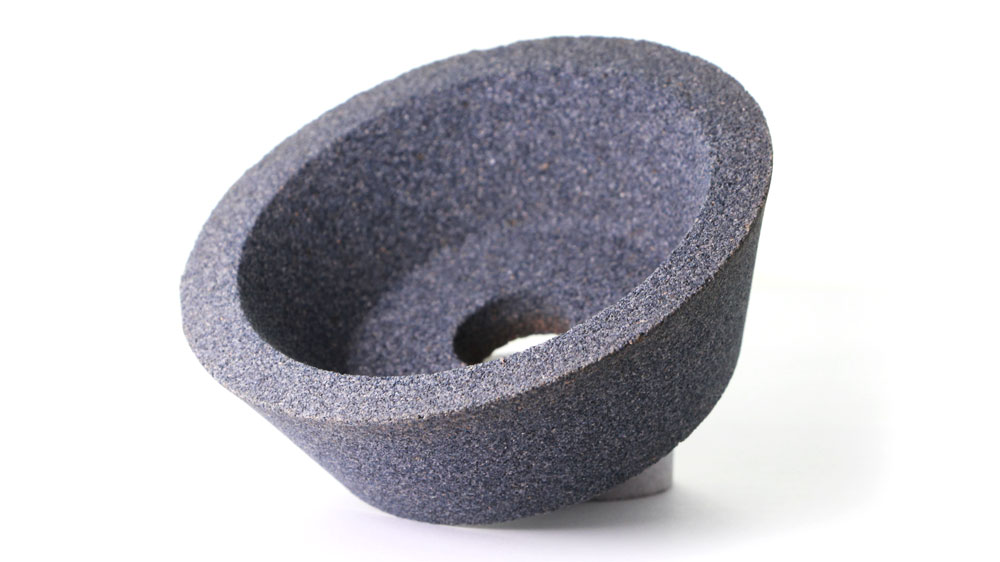
Single-Crystal Aluminum Oxide:
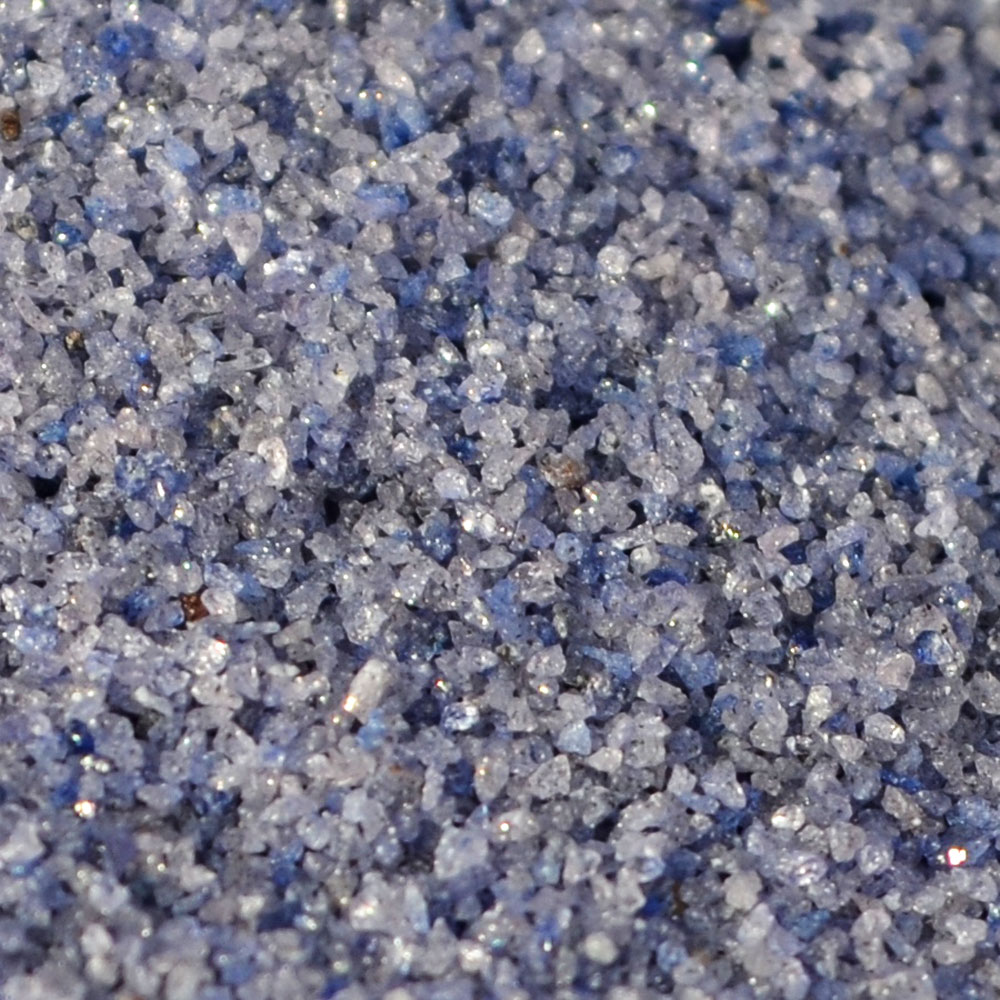
Black Silicon Carbide:
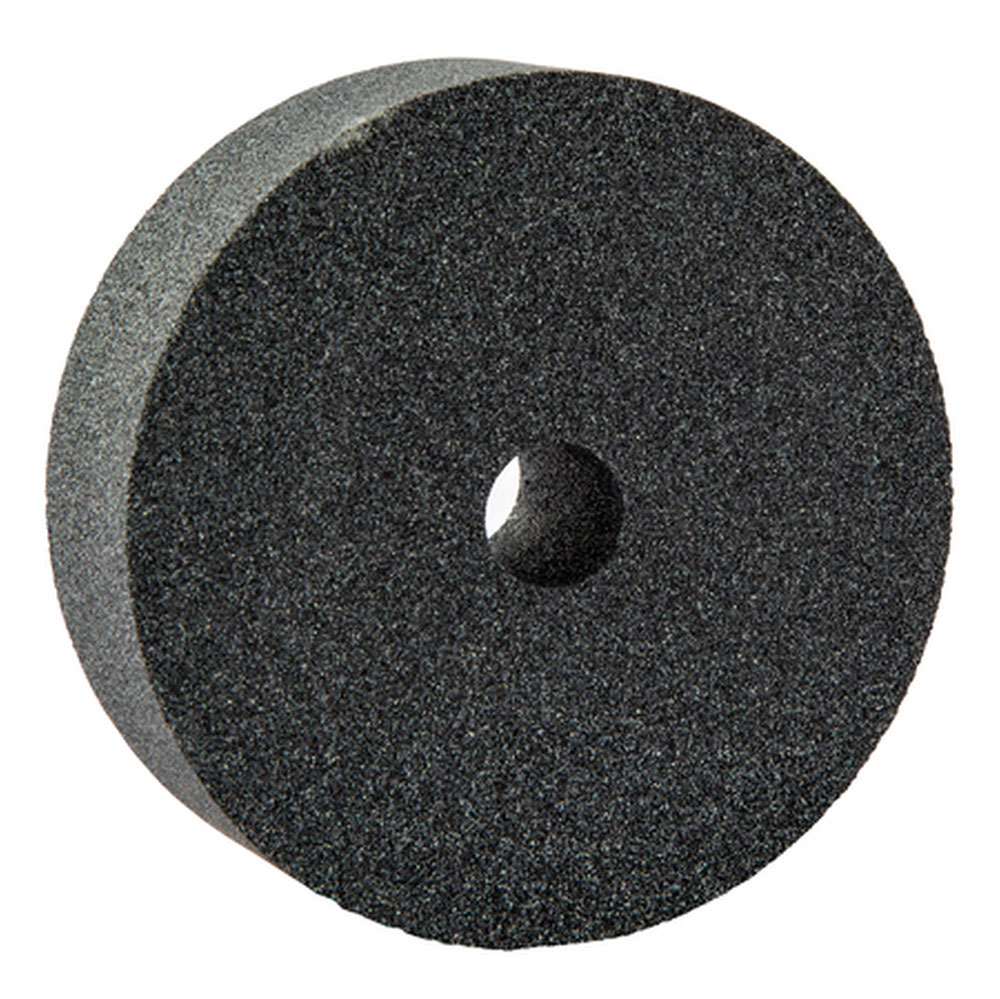
Black Silicon carbide is produced at high temperature in an electric resistance type furnace with quarts sand and petroleum coke. Silicon carbide abrasive, also known as moissanite, can also be called emery or refractory sand. It is a man-made substance. It is made by high-temperature smelting of raw materials such as quartz sand, petroleum coke (or coal coke), and wood chips in a resistance furnace.
Black Silicon Carbide (SiC) is an extremely hard man made mineral that possesses high thermal conductivity and high strength at elevated temperatures. SiC has a modulus of elasticity of 410 GPa, with no decrease in strength up to 1600°C, and it does not melt at normal pressures but instead dissociates at 2600°C.
Green silicon carbide:
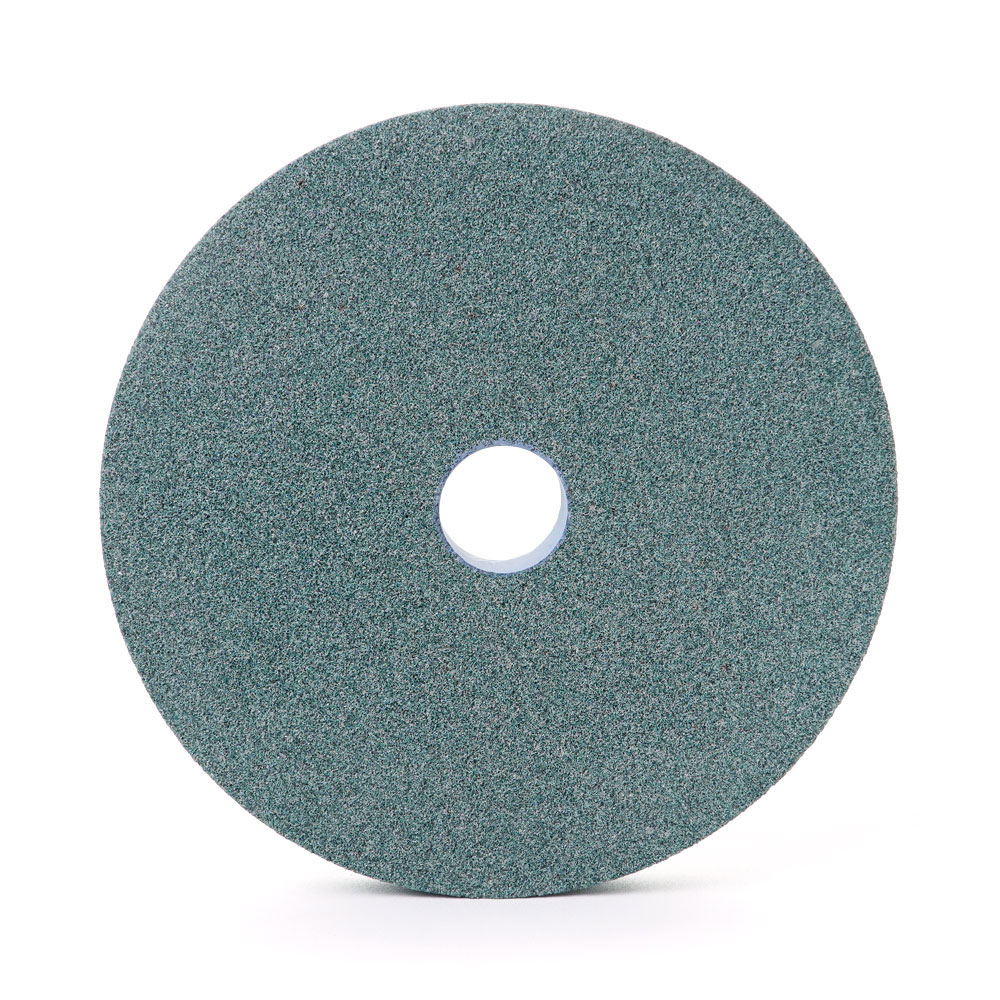
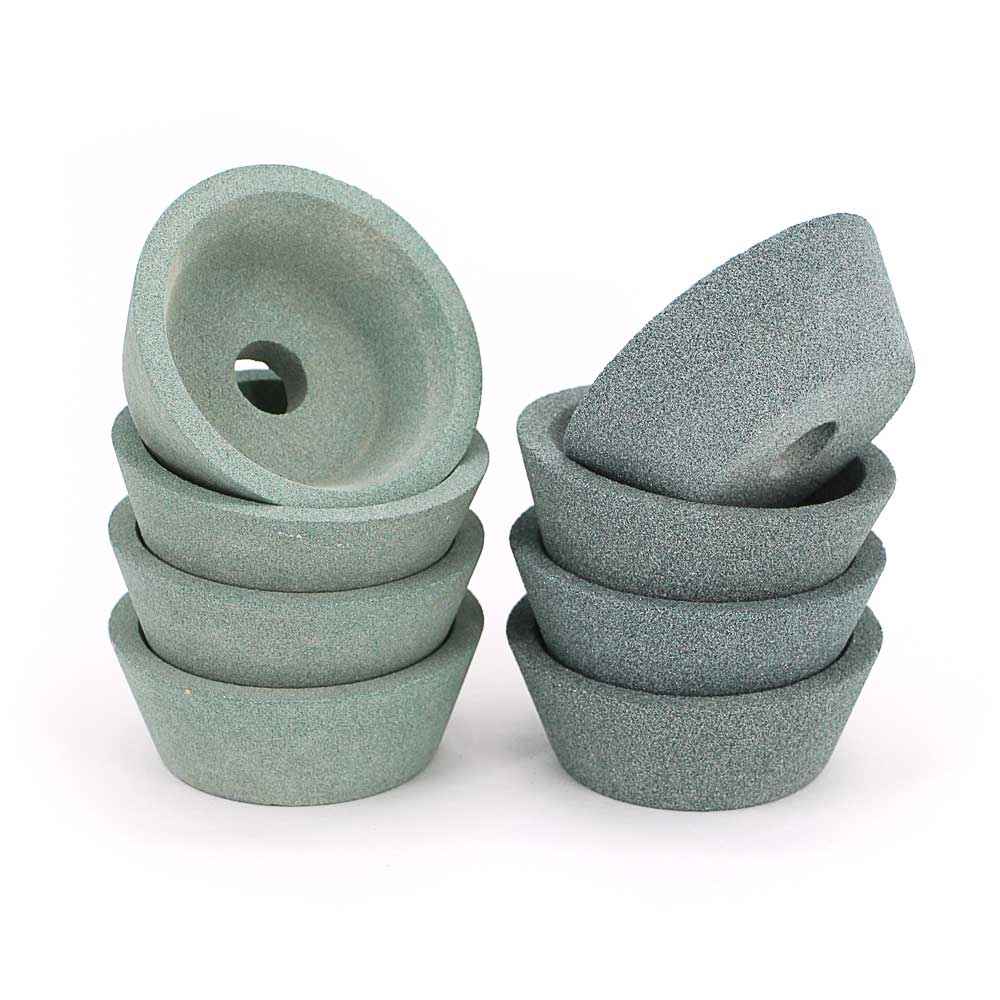
Green silicon carbide is a non-metallic mineral product produced by high quality quartz sand and petroleum coke at the high temperature over 1800℃ in the electric resistance furnace. It contains more than 99% of SiO2,good self-sharpness, and its toughness is slightly lower than black silicon carbide.
The fused green silicon carbide block is common known as emery and formed different sizes of products after crushing, acid and alkali washing, magnetic separation, and screening or water-separation. The silicon carbide is semi-conductor, 9.5 of Mohs hardness, with good thermal conductivity and oxidization resistance performance at high temperature. Our silicon carbide has advantages of high hardness, low expansion coefficient, and good thermal conductivity etc.
These materials can be formed into different types of grinding wheel for different usage:
Different Types of Conventional Grinding Wheels
Surface Grinding Wheels:
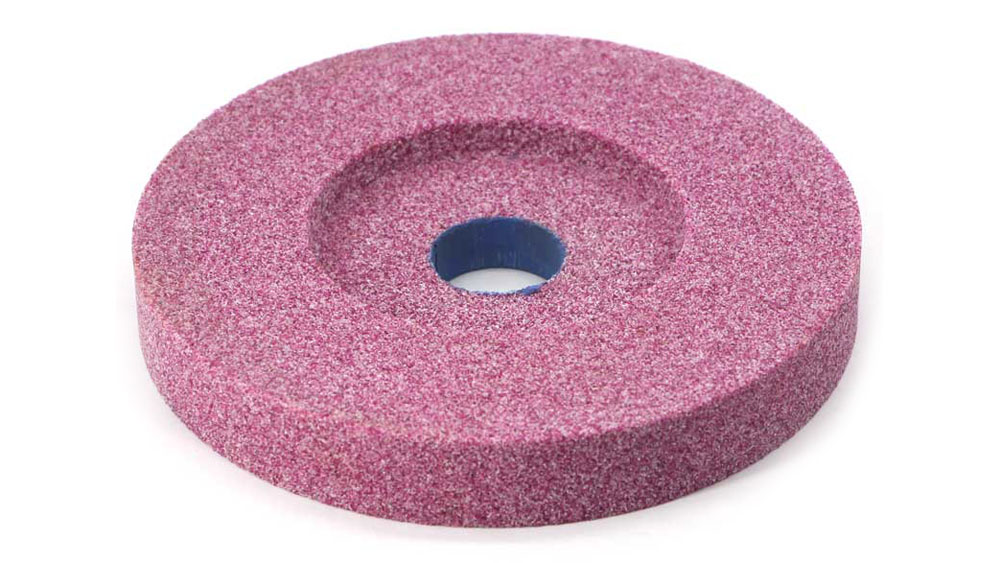
Surface grinding is done on flat surfaces to produce a smooth finish. It is a widely used abrasive machining process in which a spinning wheel covered in rough particles (grinding wheel) cuts chips of metallic or nonmetallic substance from a work piece, making a face of it flat or smooth.
Surface grinding wheels are abrasive wheels that remove material from metal, wood, glass, and other surfaces more efficiently than hand sanding. Sometimes called surface grinders, they are used in conjunction with stationary and portable grinders and covered in an abrasive grit designed to grind specific surfaces.
Straight grinding wheels are designed to grind only on their faces and are for use with bench grinders, pedestal units, and surface grinder machines. Recessed grinding wheels also grind on their faces and have a recessed center which allows them to fit on a machine spindle flange assembly. Use surface grinding segments to grind flat stock or flat surfaces.
Surface grinding wheels and segments are a universal choice for heavy, rapid stock removal and production work to precision tolerance operations. Our surface grinding wheels come in a variety of abrasive grain types and bonds and can increase grinding performance anywhere from 100-600%.
Centerless grinding wheels:
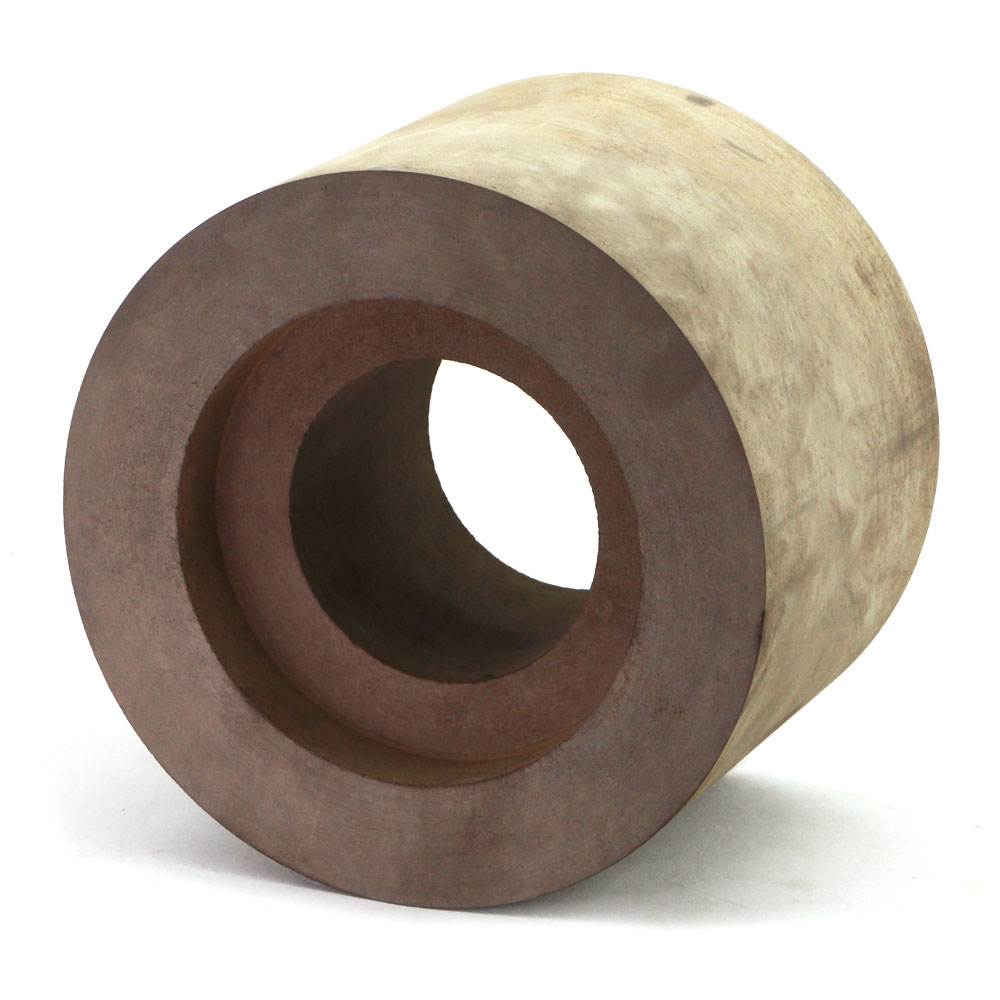
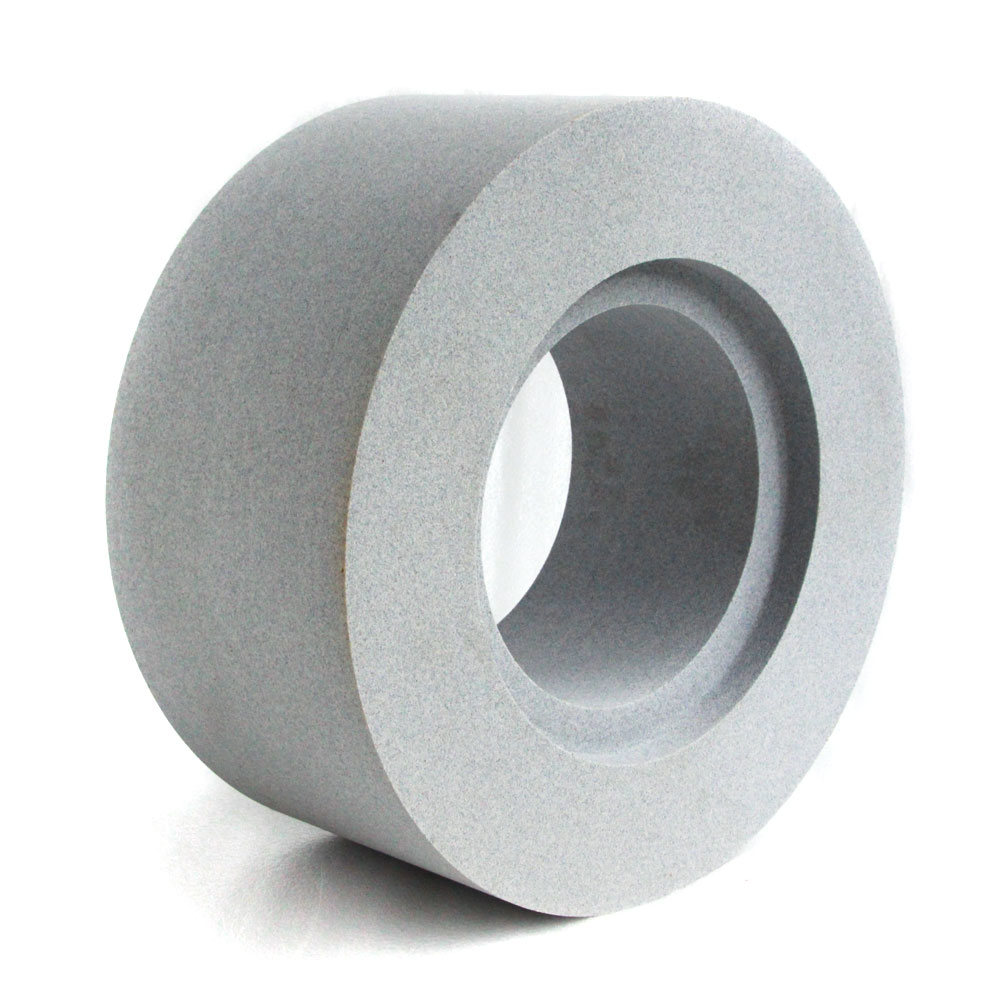
Centreless grinding can perform excellent roundness of the workpiece. The workpiece is supported by a work rest blade and set between a rubber regulating wheel that rotates the workpiece and a rotating grinding wheel. Sometimes both conventional grinding wheels will be used on centerless grinder. In centerless grinding, regulating wheel control and driving the workpiece, the grinding wheel do the grinding effects on the workpiece.
In centerless grinding, the workpiece is held between two grinding wheels, rotating in the same direction at different speeds. One grinding wheel is on a fixed axis and rotates so that the force applied to the workpiece is directed downward.
Cylindrical Grinding Wheels:
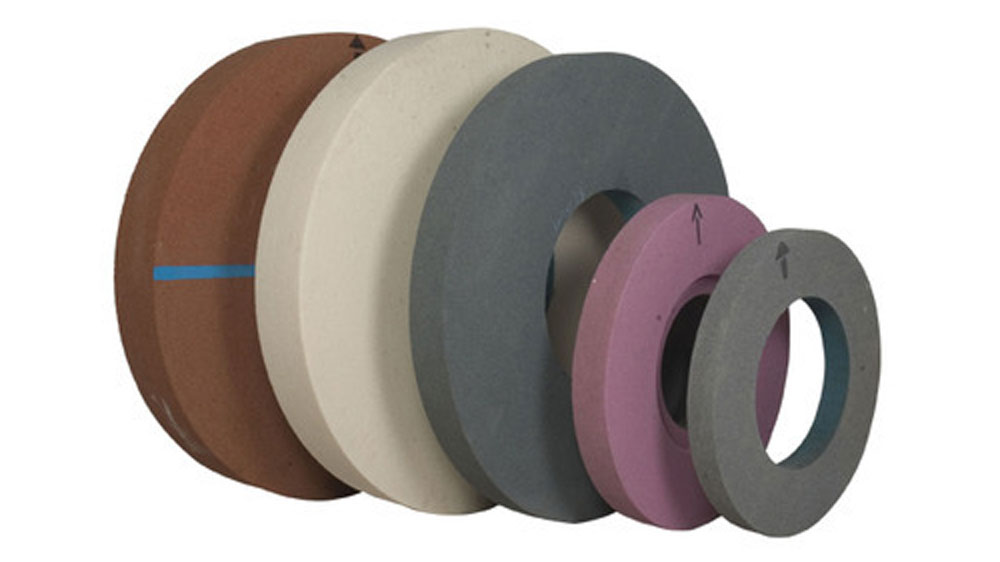
Cylindrical grinding wheels are typically used in the transportation and tool room industries and are ideal for medium to heavy stock removal. If you are concerned with wheel life and total per-part grinding costs, our cylindrical grinding wheels increase production and decrease cost.
Cylindrical grinding wheels are used to shape the object which may or may not be cylindrical in shape having an axis of rotation. And of course cylindrical grinding stone rotates by motorized attachment to overcome the moment of inertia and rotate it at the desired speed. The work-piece may be conical as special farm cylindrical wheels are used for grinding works which are held between center & chucks.
The bonds which have been specially developed for precision grinding wheels are used for their production, which runs cool enough to avoid cooling/cutting oils used by the consumer. Apart from it, these bonds do not overheat the job and hence gives the desired finish and cutting simultaneously. Moreover, the per-component cost is much lower than that of the other precision grinding wheels available in the market.
Internal grinding wheel:
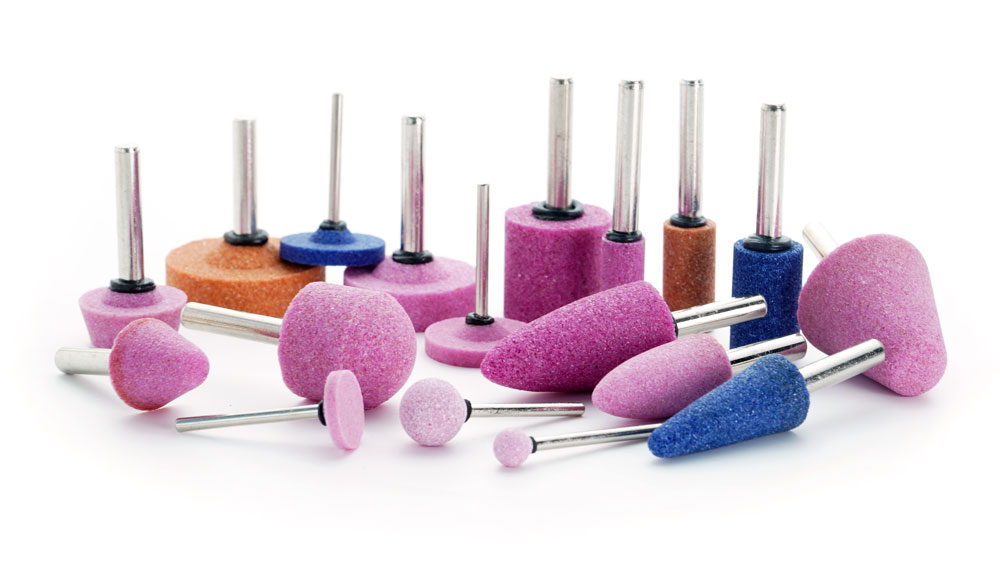
If you still have any questions about conventional grinding wheels of aluminum oxide and silicon carbide, contact Mrbrianzhao, he will give you best guidance to choose the most suitable wheels for your usage.