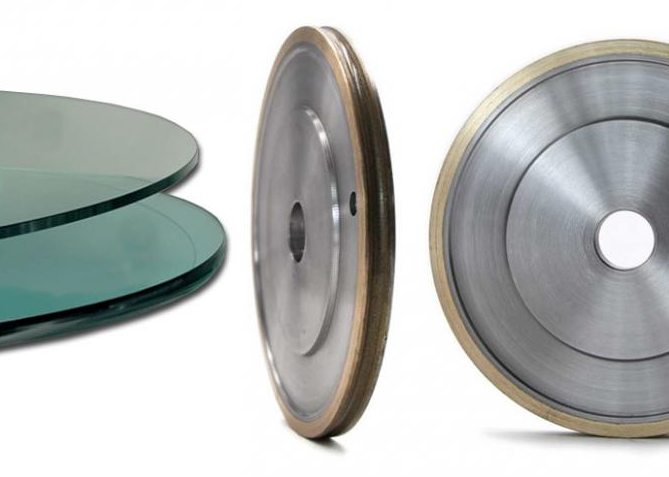
- 1. Type of Grinding Wheel and Abrasive Selection
- 2. Grinding Wheel Hardness
- 3. Grinding Wheel Grit Size
- 4. Installation and Balancing of the Grinding Wheel
- 5. Clamping and Positioning of the Workpiece
- 6. Dressing of the Grinding Wheel
- 7. Grinding Machine Accuracy and Stability
- 8. Rigidity and Stability of the Grinding Machine
- 9. Grinding Process Parameters
- 10. Material Properties and Stability of the Workpiece
- 11. Cooling System
- 12. Selection and Use of Grinding Fluid
- 13. Thermal Deformation During Grinding
- 14. Cutting Force During Grinding
- 15. Operator Skill Level
- 16. Maintenance of the Grinding Machine
- 17. Environmental Conditions
- Conclusion
1. TYPE OF GRINDING WHEEL AND ABRASIVE SELECTION
Various abrasive wheels can be used for grinding different materials. One good example of this is the tough and strong aluminum oxide which performs best on steel, whereas silicon carbide will work well on ceramics. Choosing the right abrasive means that the grinding wheel needs to do its job but is not glazed or worn out too quickly to be effective. A properly matched abrasive allows a user to control it. Therefore, it offers a based operating manner for achieving dimensional accuracy.
2. GRINDING WHEEL HARDNESS
Grinding wheel hardness is the measure of the holding strength of the abrasive grains by bonding material. This is the junction of bond strength and the grain release that is essential. A very hard wheel (the one having the highest bond) preserves the pre-set form the best and its result is the closest tolerance. It might be so that it will be too hard, which will skip the grinding of material and the grains by attrition will be covered with the waste and will not be able to expose the fresh cutting edges. The increased grinding force, burning of the workpiece, and reduced accuracy are the most common problems out of this situation.
However, a soft wheel, which is more of a weak bond, can throw away the dull abrasive grains without having to wait for the users to expose them again. This is a good solution for grinding hard materials that erode abrasive grains quickly. Yet a very flexible wheel can lose its form very fast. This would make it hard to keep the workpiece in the correct dimensions for the required grinding.
The key lies in finding the best hardness for the specific application that you have. For example, grinding softer metals such as aluminum may be assisted by a harder wheel to keep its form and meet tolerances tightly whereas a softer wheel is necessary for the process of material removal and self-sharpening in the grinding of harder materials such as tool steel.
3. GRINDING WHEEL GRIT SIZE
The size of the grains of abrasive, or the said grit of abrasive particles is the main factor influencing the surface smoothness and the accuracy of achieving grind. Often, material removal fast may be compared to sanding with coarse sandpaper; on the other hand, slower material removal may be depicted in sanding with fine sandpaper.
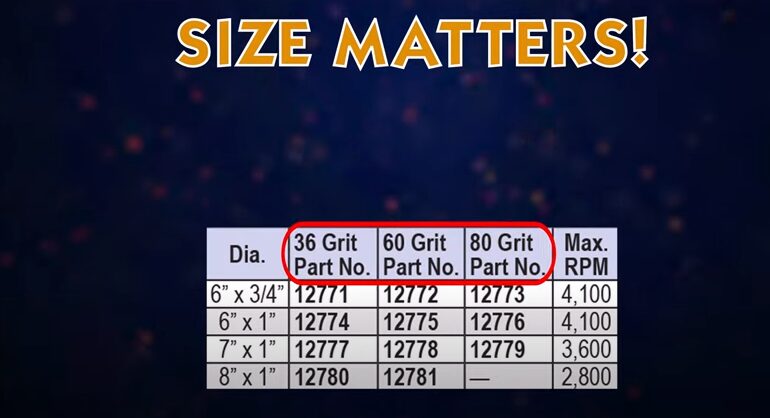
The first kind of abrasive wheel in the former case with a larger grit size will result in higher material removal but with a rougher surface that has a wider range of potential dimensional deviations. On the contrary, the second kind of abrasive wheel with a finer grit size will cut the material more slowly but will leave it smoother and come out in a stricter valid supply.
To get the right grit size, you have to first decide what is more important to you- higher material removal rates, perfect surface finishes, or tighter dimensional tolerances. A higher grit size for coarse grinding and stock removal chores might also be considered. However, the more precise the grinding-to-the-tight-tolerance process is, the finer the grit size that is to be worked with.
4. INSTALLATION AND BALANCING OF THE GRINDING WHEEL
Image a spinning disc which has high speed as the grinding wheel. Even the smallest unbalance might lead the wheel into an unstable spinning motion, and consequently the vibrations, which are transitive, will spread through the product and the machine. This distortion of the grinding path is reflected in the production of excessive numbers of products that do not meet the specified dimensional tolerances, the damaging of some parts or the machine warranty.
Correct mounting is the key in safely fitting the grinding wheel to the spindle of the machine so that it is dead parallel to the mounting surface. Besides, very few balancing holes are drilled into wheels, and the balance weights, if any, are attached by welding. This means a very small piece can make a huge difference.
5. CLAMPING AND POSITIONING OF THE WORKPIECE
Just like a perfectly balanced wheel that is securely clamped and correctly positioned allows for greater grinding precision, a perfectly clamped and properly positioned workpiece is similarly critical in the grinding process. Affixing the workpiece is a prerequisite for preventing any movement of the workpiece with respect to the grinding wheel. Afterward, the grinding wheel removes the chosen surface leaving the blank piece of material unaffected.
6. DRESSING OF THE GRINDING WHEEL
A kind of a grinding wheel will only be efficient, provided that its grains will be constantly replenished with new and sharp ones. Typically, on the part that contacts the workpiece, grinding wheels tend to become dull. Utilizing a dressing tool on a grinding wheel is to remove the worn-out abrasive grains and expose several cutting edges.
Overdressing causes the removal of excessive abrasive material which in turn, decreases the life of the grinding wheel making it unable to maintain its shape. This might result in grinding path inconsistencies and thus the grinding accuracy would be decreased. However, what makes it a real balancing act is the choice of the right dressing frequency – not too often to overpressure the wheel, but frequent enough to maintain the edges’ sharpness.
7. GRINDING MACHINE ACCURACY AND STABILITY
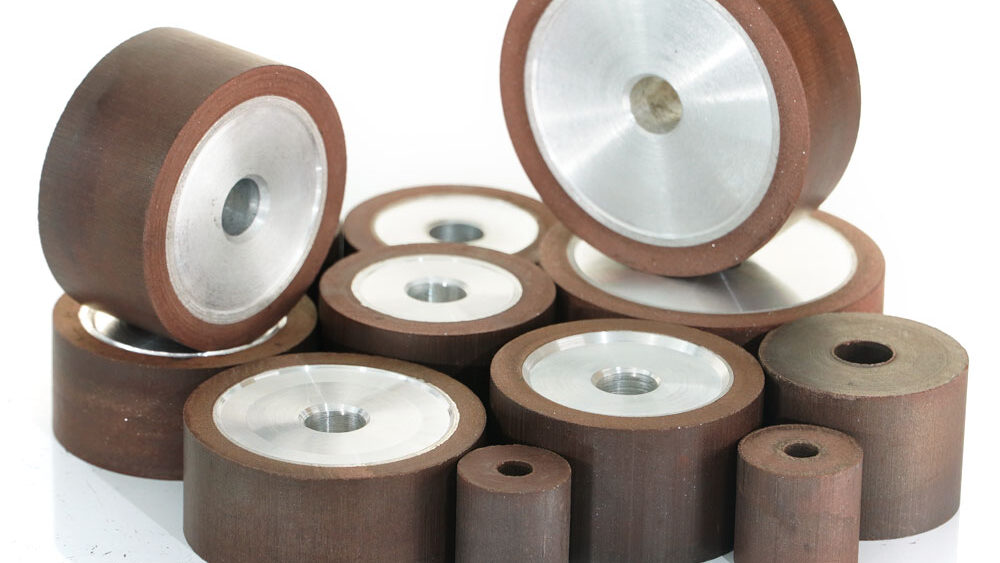
Contemporary grinding machines are a representation of the immense progress in engineering. They are supported by highly adaptive control systems and precision components. These specifications make today’s grinding machines far better than older machines in terms of grinding accuracy. The control systems with higher precision are able to ensure that the grinding wheel is in the specific position relative to the workpiece for the material removal to happen where is needed. Additionally, the automatic compensation for the wheel wear and the wheels can move in a more stable and precise manner.
8. RIGIDITY AND STABILITY OF THE GRINDING MACHINE
Think about a wobbly table that is trying to hold a set of fine china plates and contrast this with the behavior of a grinding machine. The machine’s overall rigidity and stability directly impact grinding accuracy. The unyielding machine with near-zero deflection under load provides a guaranteed pathway of precision cuts. A soft machine with a great deal of movement due to the force of grinding can even cause distortions that make the grinding wheel get out of line and thus ruin the dimensional accuracy.
9. GRINDING PROCESS PARAMETERS
- Grinding Speed: The rotation speed of the grinding wheel is an essential parameter that decides the material removal rate and surface finish. At higher speeds, the tool removes material more quickly but at the same time produces heat and vibration that may affect the accuracy of the product.
- Feed Rate: The term describes the time at which a workpiece is loaded and the grinding wheel is forced to pass it. At a slower feed rate, a more accurate grinding of a material is allowed, but a longer time is required. A slow feed rate is conducive to accuracy, but it extends the time. On the other hand, a quick feed rate may be less precise but it is more suitable for higher productivity.
- Grinding Depth: This one refers to the amount of material that is gotten rid of with the help of the grinding wheel for each pass. A smaller depth allows for better control but takes longer to remove material. A deeper depth, on the other hand, allows the process to be faster, but it requires a stiffer machine and better control for nearer measurements. It all depends on the process and material properties.
- Coolant Use: The use of coolant in the grinding process is an excellent idea as it helps to lower heat thus prolonging the lifespan of the workpiece and grinding wheel. This highly efficient method supports grinding accuracy and surface finish.
10. MATERIAL PROPERTIES AND STABILITY OF THE WORKPIECE
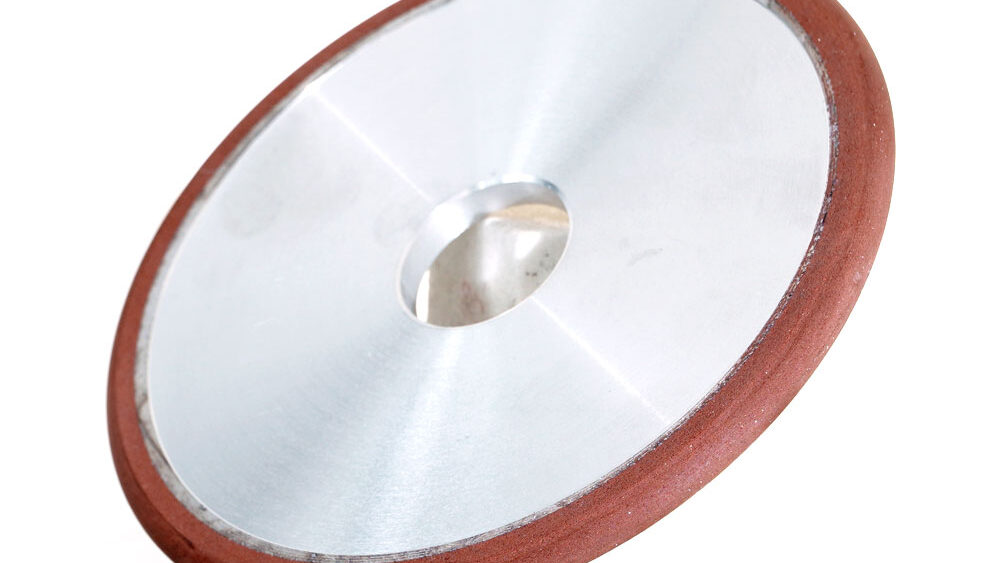
The characteristics of the material you are grinding will greatly influence its reaction to the grinding treatment. For example, chipping or cracking of glass may occur if the grinding forces are excessive due to the hardness and brittleness of the material. For example, in the case of soft, ductile materials such as aluminum, they might become-deformed-or-smeared-during-the-ground-process-if-they-are not-strengthed properly.A proper perception of these properties thus enables the use of the most suitable parameters and techniques for grinding that will serve as a sure way of reducing the risks and thus getting precise results.
Also, important to working the piece cleverly during grinding operations. A workpiece that has an inadequate or not correctly secured clamping or which has already internal stresses will start to vibrate or warp during the grinding process. This vibration is likely to push the grinding wheel off its desired path, resulting in the irregular and inaccurate final dimensions. The main steps to be taken for ensuring the workpiece’s security, that it is properly supported, and that the amount of the internal stresses is within the permissible limit are critical for achieving the required grinding accuracy.
11. COOLING SYSTEM
The heat generated during the grinding process is an enemy of the accurate grinding ally. It is getting hot, and this is the case with the thermal deformation that is produced all over both workpiece and grinding wheel. Lots of inconsistencies and compromise the final dimensions and burning the workpiece is among them. The cooling system that is functioning can serve as an inhibitor of these issues.
By using a coolant while grinding, you could bring the temperature down markedly in the grinding zone. This way, it can be avoided that the workpiece and the grinding wheel often are malformed because of the heat and maintain their shapes and therefore brings about a better grinding accuracy. Different coolants have distinct attributes. High silicone content ones have excellent adhesion and can therefore aid in greater heat resistance in the grinding zone.
12. SELECTION AND USE OF GRINDING FLUID
It is not only the cooling factors that a grinding fluid performs but it is also a source of the lubrication process and the evacuation of swarf. Beside the proper cooling, the lubrication nature and the ability of a fluid to remove the chips from the surface should be carefully considered to help improve your grinding accuracy.
For instance, using a water-based lubricant while grinding some materials has its benefits. These coolants provide maximum cooling effect and are known to be nature-friendly worldwide. On the other hand, when grinding other materials, a synthetic coolant may be a more effective choice. Synthetic coolants are able to achieve high-performance applications in providing better lubrication and chip removal processes. However, the right distribution of the grinding fluid is also necessary. The fluid must be directed onto the grinding zone in such a way that it takes away the heat and chips without disturbing the grinding process.
13. THERMAL DEFORMATION DURING GRINDING
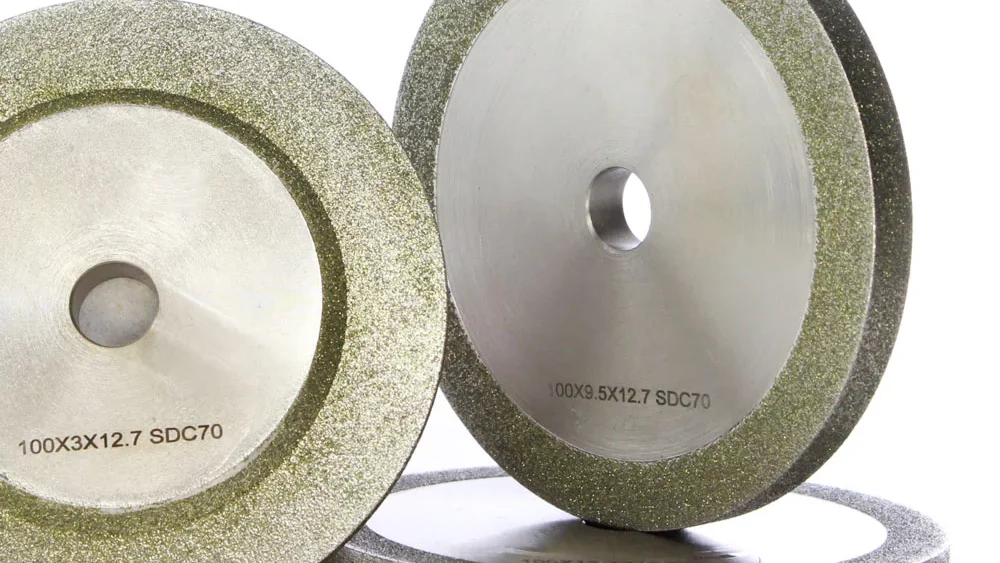
In order to minimize thermal deformation, a variety of methods can be used, among which we can mention, the installation of a very efficient cooling system, besides the right selection of grinding parameters (like speed and depth of cut) in order that heat generation is minimized, and also the choosing of the grinding wheels which are least susceptible to thermal alteration.
14. CUTTING FORCE DURING GRINDING
The primary idea of grinding, in fact, is the grinding wheel “cutting” away the material from the workpiece. The force needed to accomplish this cutting action is known as the cutting force. The higher the cutting force, the faster the material can be removed, but it also has a negative impact on the grinding accuracy. At higher spinning rates, a rising cutting force may lead to such an effect that the workpiece may not bend in the way it should and as a consequence, the grinding wheel might start to move off its set path, thus the application of a reduced dimension, will be attained.
It is necessary to find a compromise between the forces of grinding and the speed of grinding. In high-precision grinding, it might be required to have the lower cutting forces and the slower grinding rates. Furthermore, a sturdy machine construction that can minimize deflection in the very high-speed grinding application becomes a vital part of the grinding process.
15. OPERATOR SKILL LEVEL
Despite the fact that the use of advanced technology and setting up of the most proper parameters are the first preconditions, remember that the main part in achieving grinding accuracy is the operator skill and experience. An experienced operator can:
- Choose the best grinding wheel and parameters, based on the material type and the desired result.
- Prepare the grinding machine for optimal process and accuracy.
- Supervise the grinding process, and if necessary adjust the settings to ensure the same result every time.
- Detect the problems that the action may affect the accuracy of such as wheel wear or workpiece vibration and then correct it.
The ability to make these educated decisions and perform these corrections while grinding can only mean that an experienced operator is no longer an amateur but a real master of the craft. Operator training offers a rather small investment; still, it has a great impact on the degree of grinding accuracy and homogeneity.
16. MAINTENANCE OF THE GRINDING MACHINE
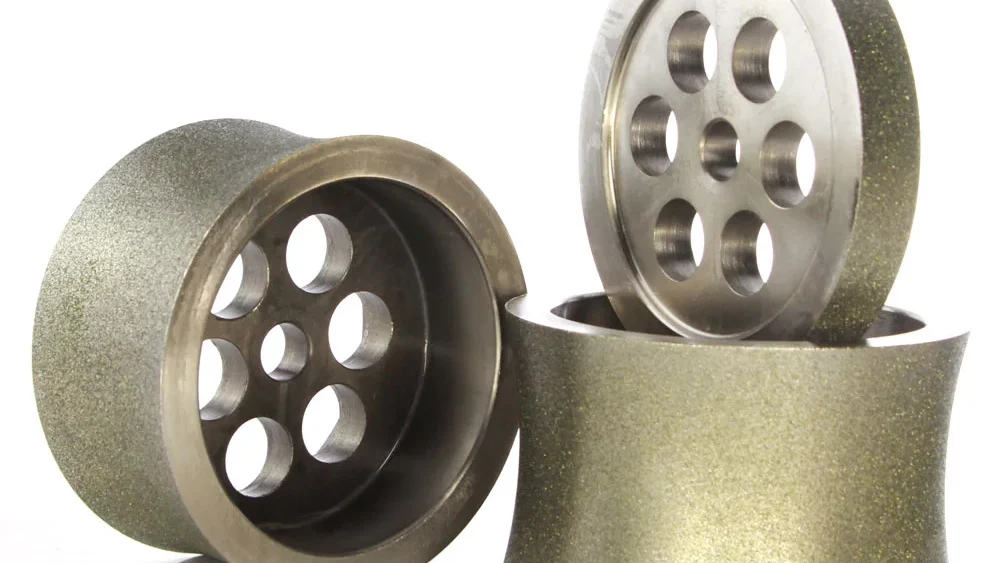
The proper maintenance includes regular inspection, cleaning, and lubrication of the machine’s components. Besides, a timely follow-up of the maintenance schedule is paramount to ensuring that the grinding machine remains in top condition. Some grinding machines even need periodical calibration to make sure their control systems do not lose accuracy. You can preclude potential problems with your grinding machine’s accuracy by being on the proactive end of the maintenance protocol and observing its continuous operation in the target manner of your pride item.
17. ENVIRONMENTAL CONDITIONS
The grinding process is a mechanical process which might be affected in many different ways if it comes under the influence of extreme temperature or humidity. High temperatures may expand the machine parts due to thermal expansion which could consequently result in the misalignment of the grinding surface and the consequential poor accuracy. The grinding wheel can similarly suffer from the humid environment and as a result of that, it would not remove material uniformly.
Conclusion