During the grinding process, not all types of grinding wheels are prone to rusting. However, those containing iron components, such as some metal-bonded wheels and certain special materials, do pose a risk of rusting under specific conditions. This is because iron components can undergo oxidation reactions when exposed to water and oxygen, leading to rust formation.
1. Conditions for Grinding Wheel Rusting
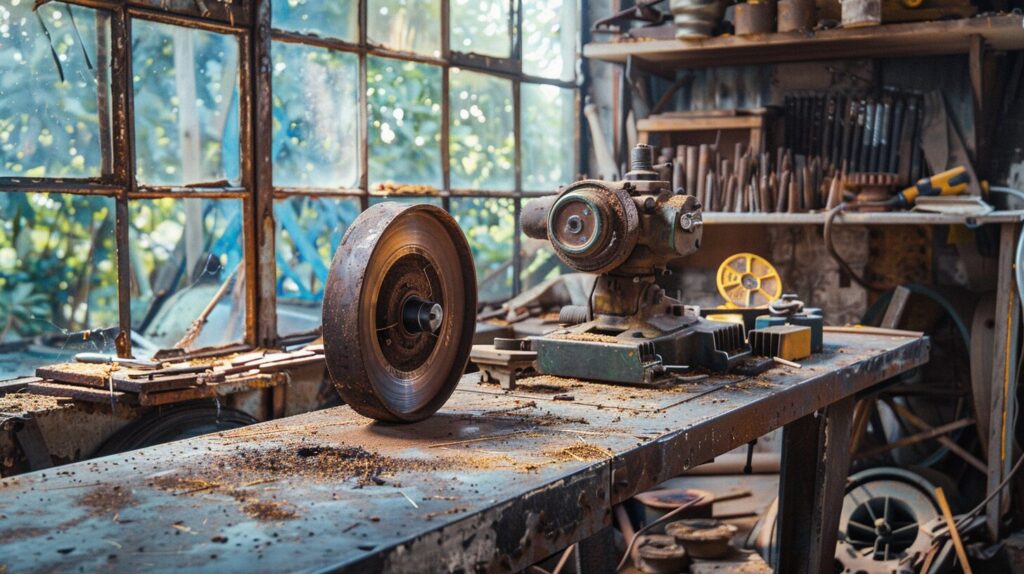
The conditions for grinding wheel rusting mainly include two aspects: environmental humidity and the material and processing of the wheel itself. In humid environments, the surface of the grinding wheel easily absorbs moisture, providing conditions for rusting. Moreover, inadequate manufacturing processes, such as improper treatment of the wheel base or insufficient rust prevention after finishing, can also increase the likelihood of rusting.
2. Impact of Grinding Wheel Rusting on Grinding
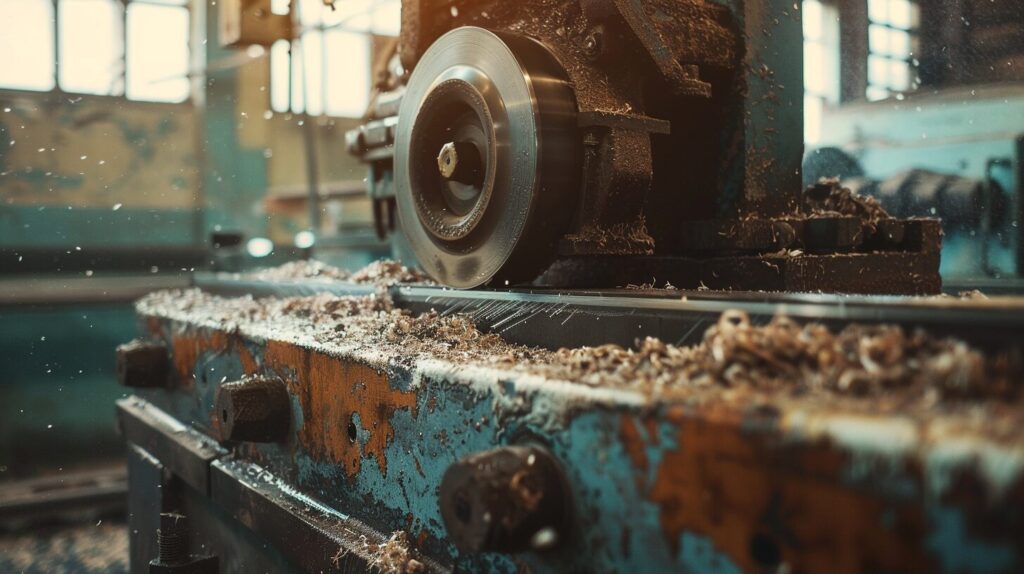
Rusting of the grinding wheel can have significant negative effects on grinding. Firstly, the roughness of the rusted wheel surface increases, leading to increased vibration and noise during grinding, thereby reducing grinding precision and efficiency. Secondly, rusted grinding wheels tend to generate heat during grinding, increasing the risk of thermal damage to the workpiece. Additionally, rusting shortens the lifespan of the grinding wheel, increasing production costs.
3. Rust Prevention Measures in Production
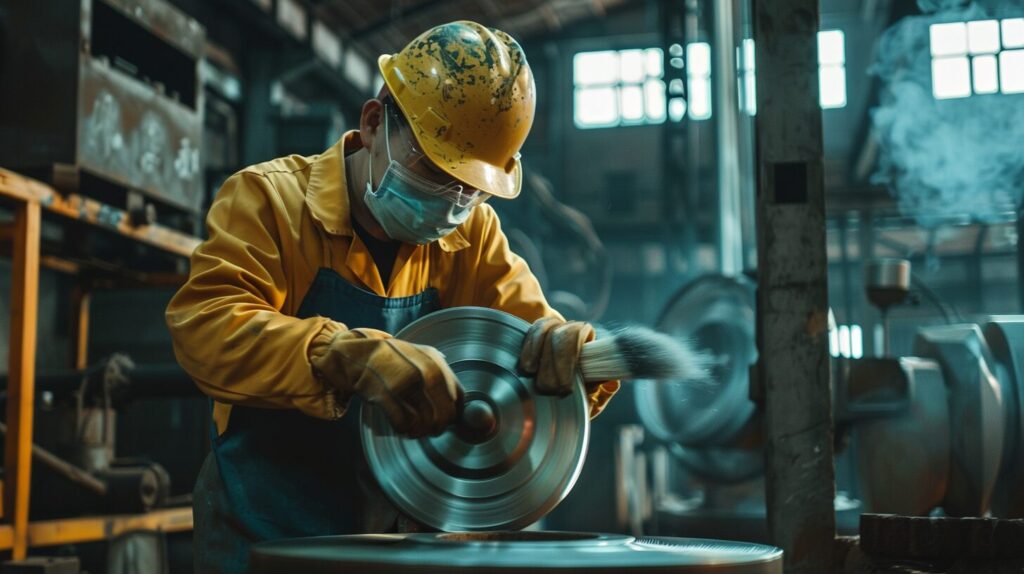
To prevent grinding wheel rusting, a series of rust prevention measures need to be taken from the production stage. Firstly, during the grinding wheel base treatment stage, materials resistant to rust, such as stainless steel, should be selected. Additionally, the base surface should be cleaned and coated with rust-resistant coatings to enhance its rust resistance. Secondly, after the grinding wheel is finished, strict rust prevention measures should be taken, such as spraying rust inhibitors or vacuum packaging, to ensure that the wheel does not rust before leaving the factory.
4. Rust Prevention Strategies in Storage and Use
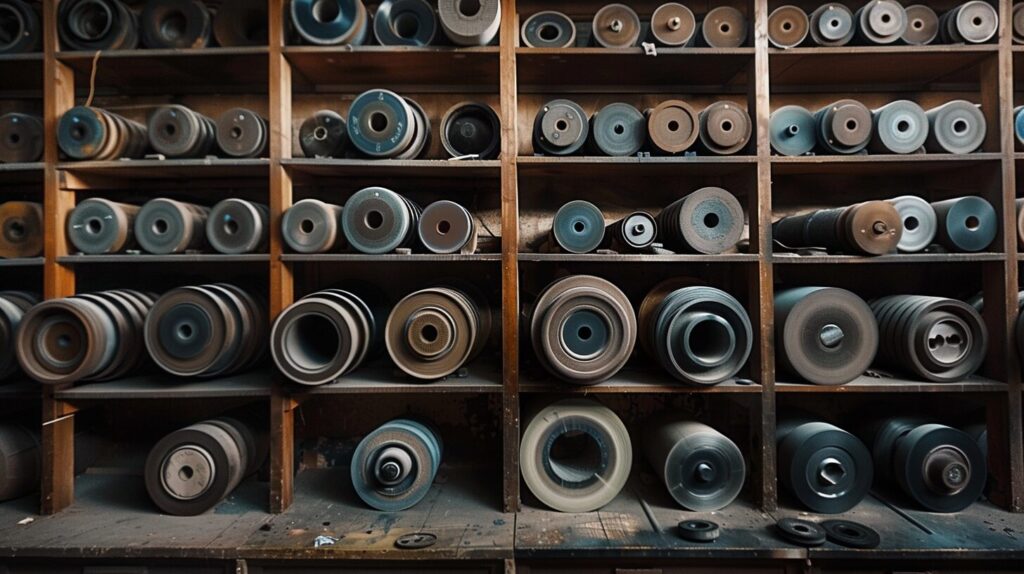
During storage, grinding wheels should be kept in a dry, ventilated environment, away from direct sunlight and humid air. Regular inspections of the wheel’s condition should be conducted, and any rust spots found should be promptly addressed. During use, keeping the grinding wheel clean and dry is essential. Before each use, check for rust on the wheel, and if necessary, lightly grind to remove rust spots. Additionally, regularly replacing heavily worn grinding wheels is an effective way to prevent rusting.
By understanding which grinding wheels are prone to rusting, the conditions for rusting, and its impact on grinding, we can take targeted rust prevention measures. From production to storage and use, attention to rust prevention measures for grinding wheels is essential to ensure their performance and lifespan. Only then can we fully leverage the advantages of grinding wheels in grinding processes, thereby improving processing efficiency and quality.